Car
Formula 1 brakes: The science of how F1 cars slow down from 360km/h
by Samarth Kanal
6min read
.jpg?cx=0.5&cy=0.5)
Formula 1 cars possess highly potent acceleration and cornering speeds that are matched by intense deceleration. In less than three seconds, an F1 car can reach a complete stop from 300km/h.
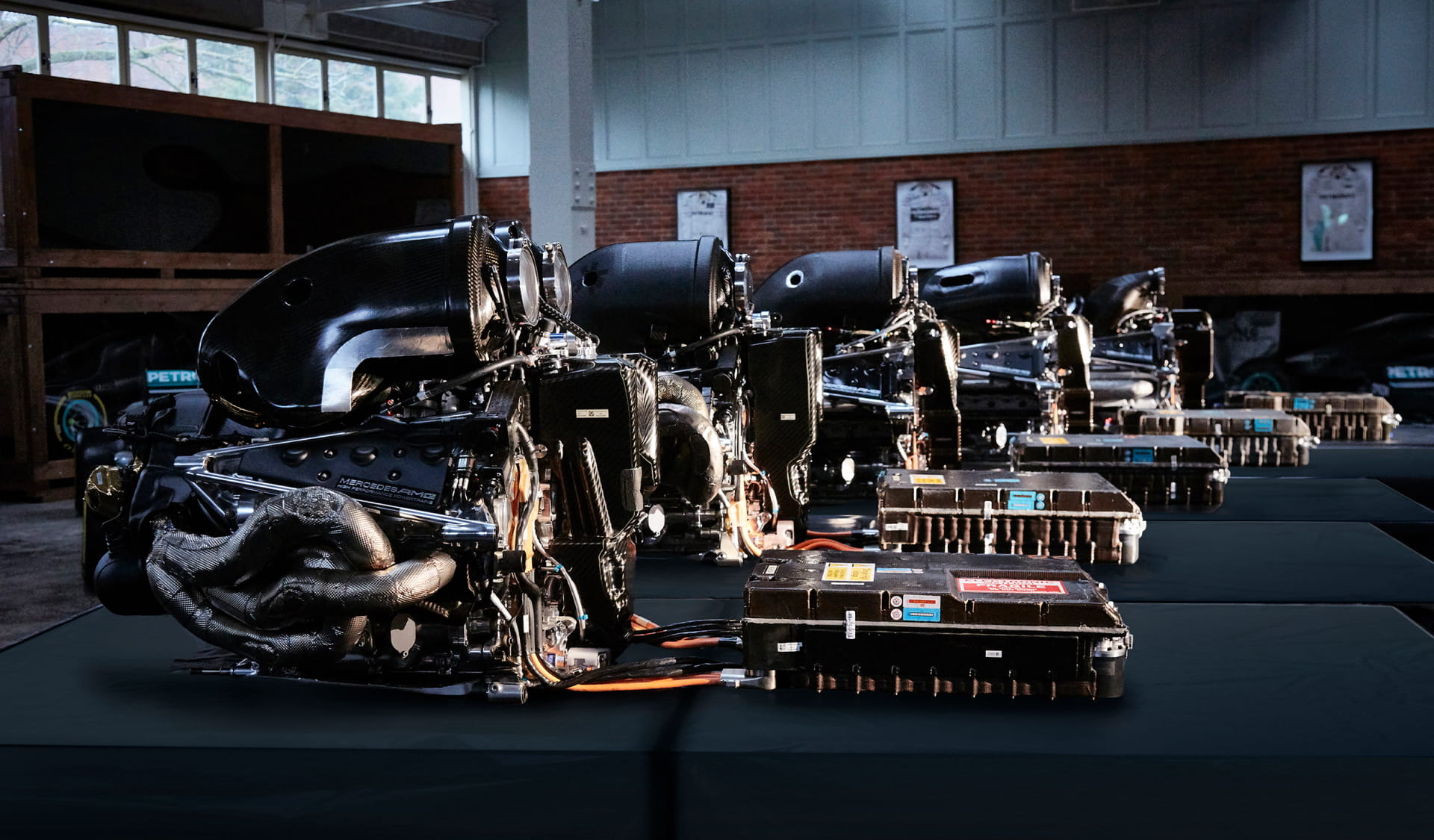
Motor, Innovation
From brutality to efficiency – how the F1 turbo engine evolved
Part of that stopping power comes from the aerodynamics that F1 cars are equipped with; higher downforce means higher drag. Of course, the braking system is the pivotal part of that.
How does an F1 car decelerate?
When a Formula 1 driver presses the brake pedal, the car can generate forces of up to 6G on the driver. This force acts opposite to the direction of travel, meaning the driver is moved forward with up to six times the normal force. The driver has to apply substantial pressure on the brake pedal in the heaviest braking zones: up to 160 kilogrammes of operating force.
That force applied to the pedal then compresses a tandem master brake cylinder that generates fluid pressure, sending compressed hydraulic fluid to brake circuits at the front and rear of the car.
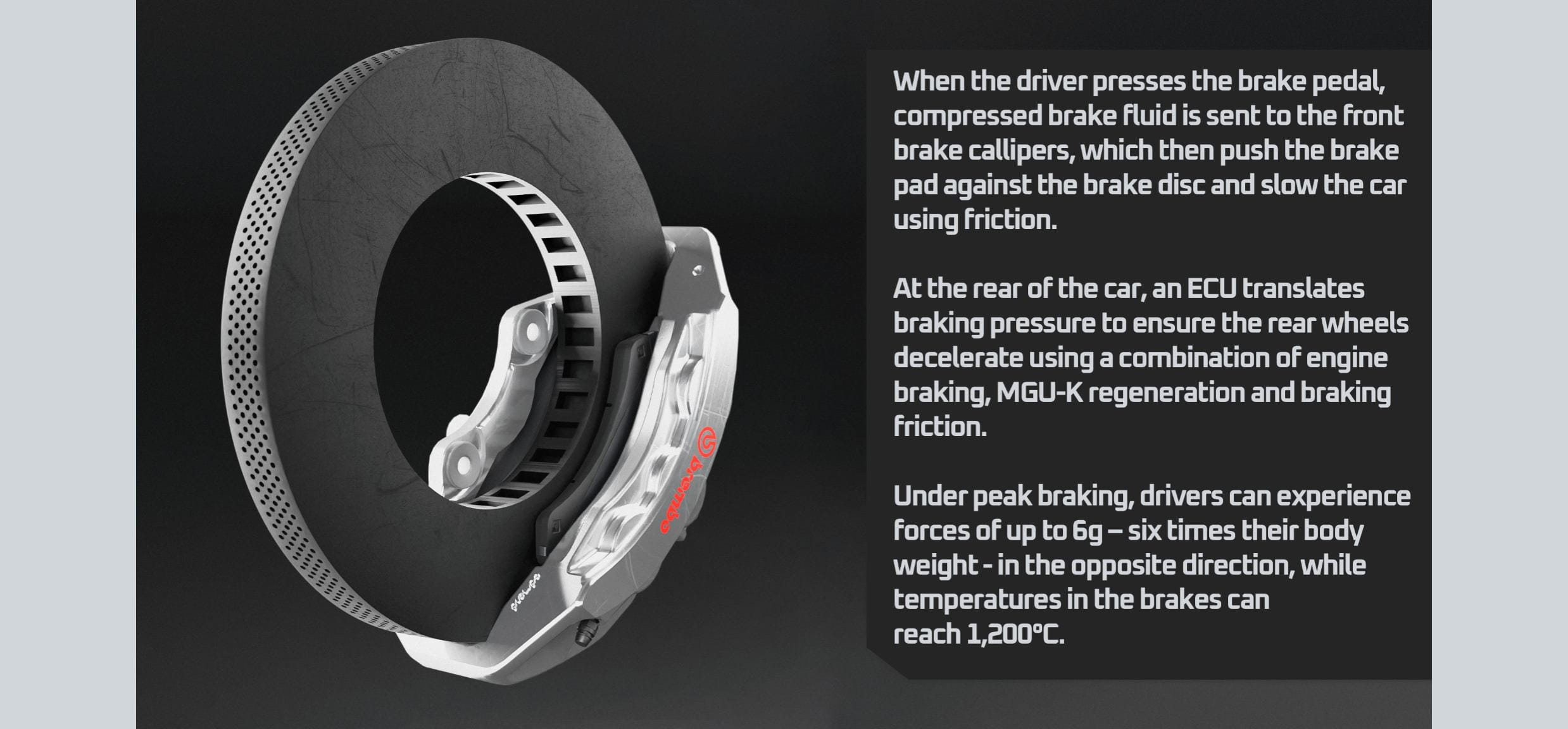
Rear brakes work differently to front brakes in an F1 car – but both work in tandem to generate intense deceleration
At the front of the car, this compressed hydraulic fluid is delivered to the brake calliper, which contains three pistons. Using the fluid pressure, these pistons (six in total at the front of the car) push the brake pad against the brake disc, and friction then slows the car down.
That friction generates temperatures of more than 1,200 degrees Celsius, which is why you might have seen glowing red brakes on older F1 cars (unlike the current generation of F1 cars, where it's hidden by wheel covers).
Deceleration can also be applied to the rear wheels using the same system, but two more devices act on the rear wheels: electrical braking from the MGU-K (Motor Generator Unit - Kinetic) and engine braking.
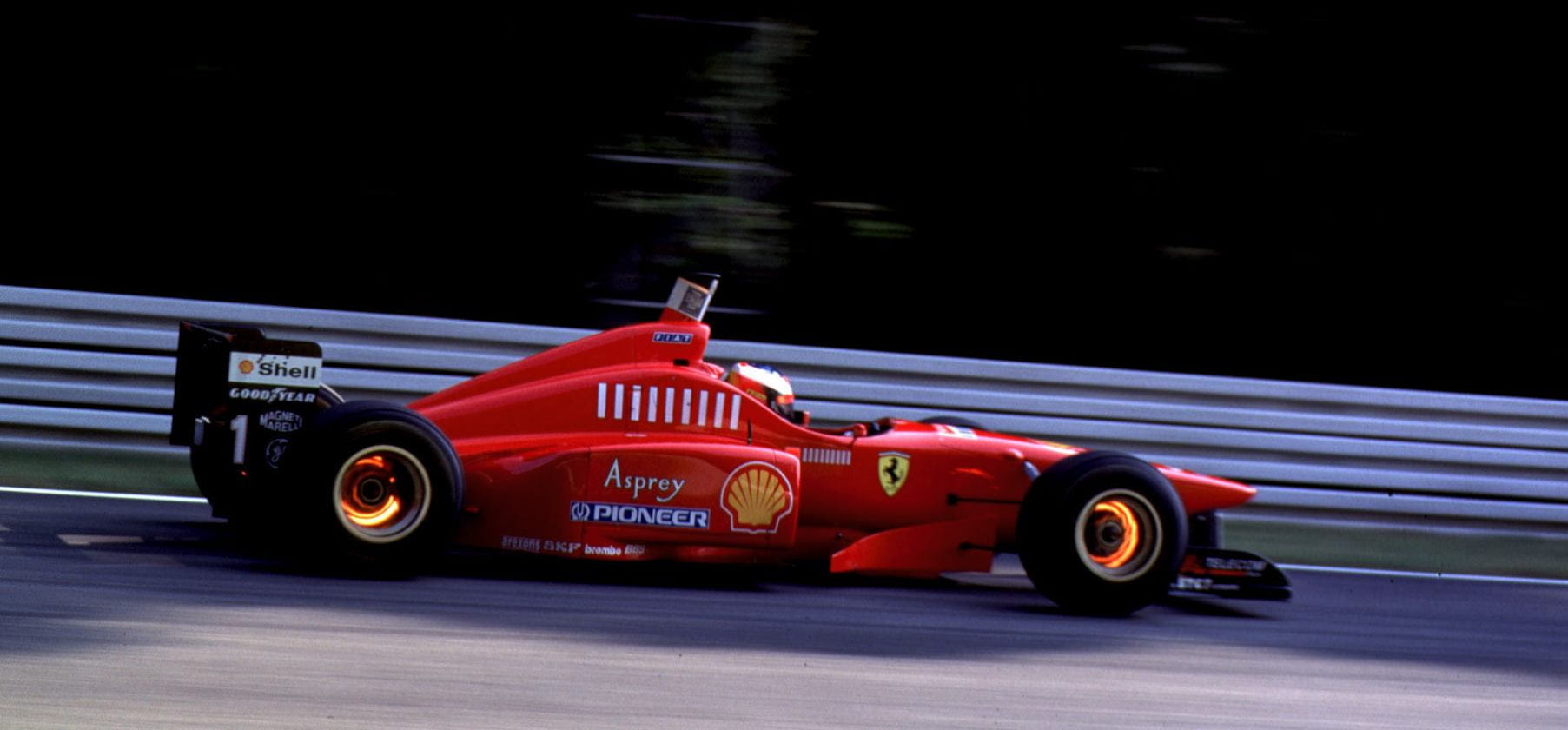
Michael Schumacher’s Ferrari F310 glowing under intense braking in 1996
Engine braking occurs when the driver lifts off the accelerator pedal. This process closes the air intake valves in the engine and creates a vacuum. This vacuum causes resistance to the pistons, which decelerates the car. Doing so can reduce rear brake wear and help control rear brake temperatures.
The MGU-K is a power unit component that converts braking energy into electrical energy. In doing so, it decelerates the rear wheels – also causing some heat, but most importantly gives the driver extra power to help overtake or defend competitor’s moves.
When the driver presses the brake pedal, all three of these deceleration systems act together via the brake-by-wire system. First, the fluid pressure is picked up by an electronic pressure sensor, which then commands the Electronic Control Unit (ECU) to apply these forces to the rear wheels of the car. A harder press on the pedal gives a larger signal to the ECU, and the rear wheels decelerate appropriately.
The driver can change engine braking and MGU-K regeneration settings using their steering wheel. They can also adjust brake bias, which changes the proportion of braking force sent to the front wheels, to account for different types of corners and conditions.
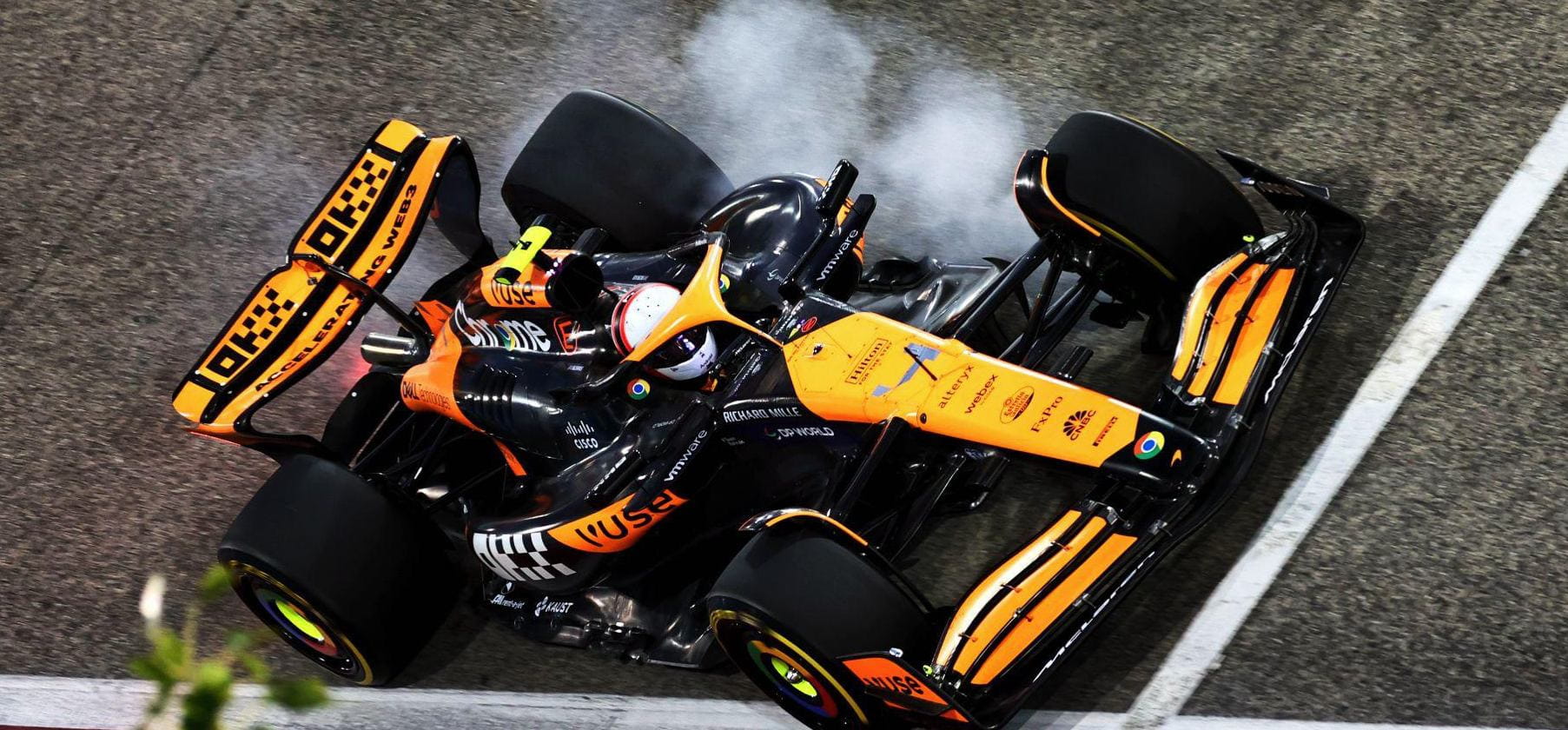
Unlike most road cars, Formula 1 cars do not have an anti-lock braking system (ABS) installed. Therefore, tyre lock-ups are common in F1. A tyre lock-up is when the amount of friction applied to the brake disc by the brake pads exceeds the amount of friction applied to the tyre by the surface of the track. This can happen for various reasons, including excess force applied to the brakes when cornering.
In case of brake-by-wire failure, there is a backup system to ensure that the car can be stopped hydraulically, without the use of the ECU.
What are braking components made out of?
Brake pedals are bespoke to each driver to ensure they can apply up to 160kg to the pedal when needed. The pedals are shaped according to the driver’s foot and are generally made out of carbon fibre. The surface of the brake pedal is coated in grip tape to ensure the driver’s foot and heel do not slip off under braking.
The four brake callipers are each made of a machined nickel-plated aluminium alloy, as are the three pistons within. Including the pistons, the calliper weighs around 2.3kg – while a road-going sports car’s brake calliper generally weighs around 5kg.
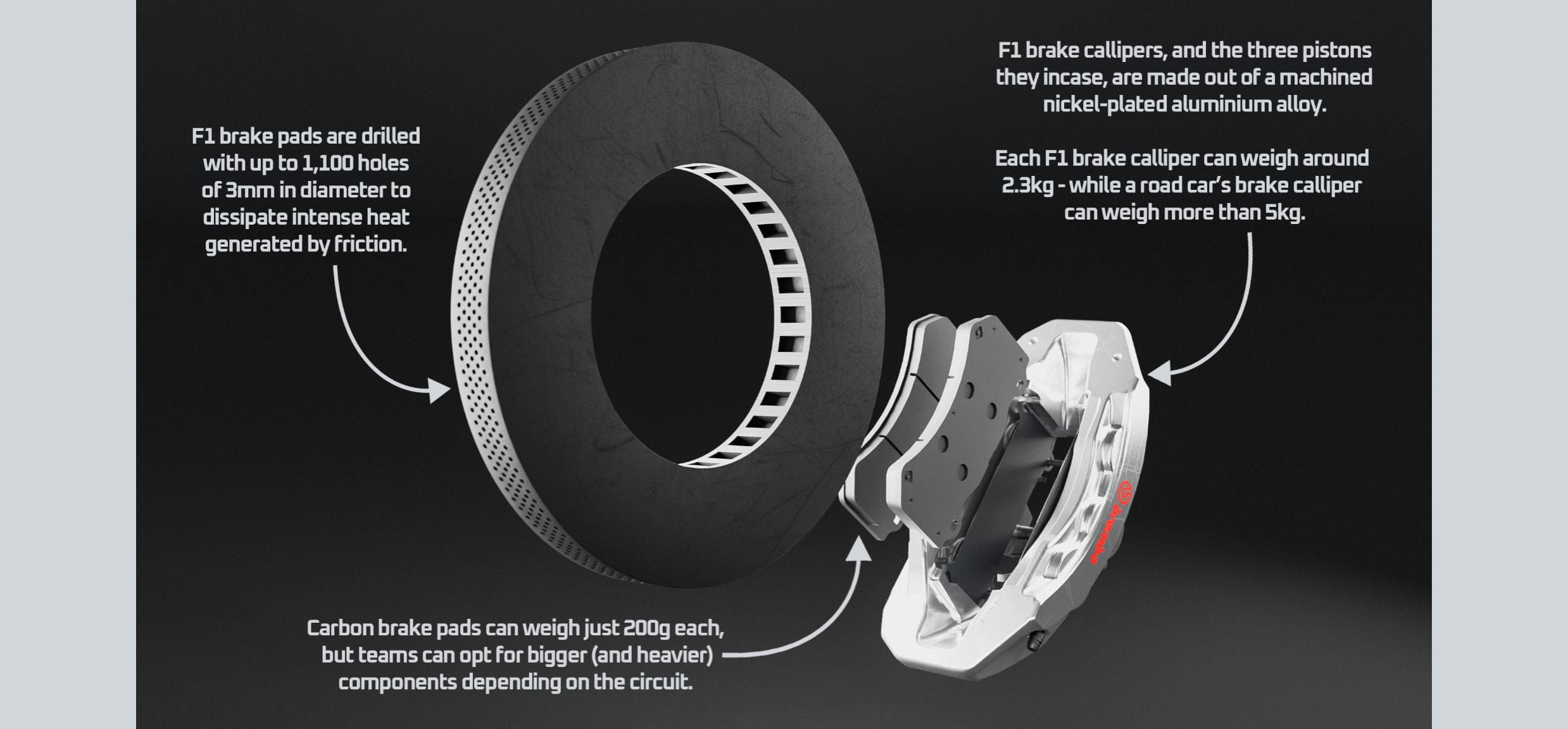
A diagram showing the components of an F1 brake: the pads, a disc, and a calliper
The brake pads are made entirely of carbon, and each 23mm-wide brake pad weighs just 200g – while a road car’s brake pads can weigh 700g. Brake pads withstand temperatures of more than 1,000 degrees Celsius, but the high friction means each brake pad needs to be changed more regularly than the callipers and disks.
Front and rear brake discs are also made out of carbon. A road car’s brake disc can weigh around 25kg compared to just 1.6kg on an F1 car. Front discs are drilled with up to 1,100 holes of 3mm each to dissipate the intense heat under braking – up to 1,200 degrees Celsius under the hardest braking zones. The brake discs are connected to the wheels with a titanium bell.
Teams may opt for different sizes of brake components depending on the circuit. For example, at the Hungaroring, where there are multiple tight and twisty slow corners, teams sometimes bring enlarged front and rear brake ducts to cope with the track's specific demands.