Motor
The rise of regenerative braking in motorsport
by Steve Rendle
8min read
/xpb_1314694_hires.jpg?cx=0.48&cy=0.64)
Formula 1 cars have used regenerative braking technology since 2009 and now multiple motorsport disciplines deploy similar systems, from sportscar racing to IndyCar.
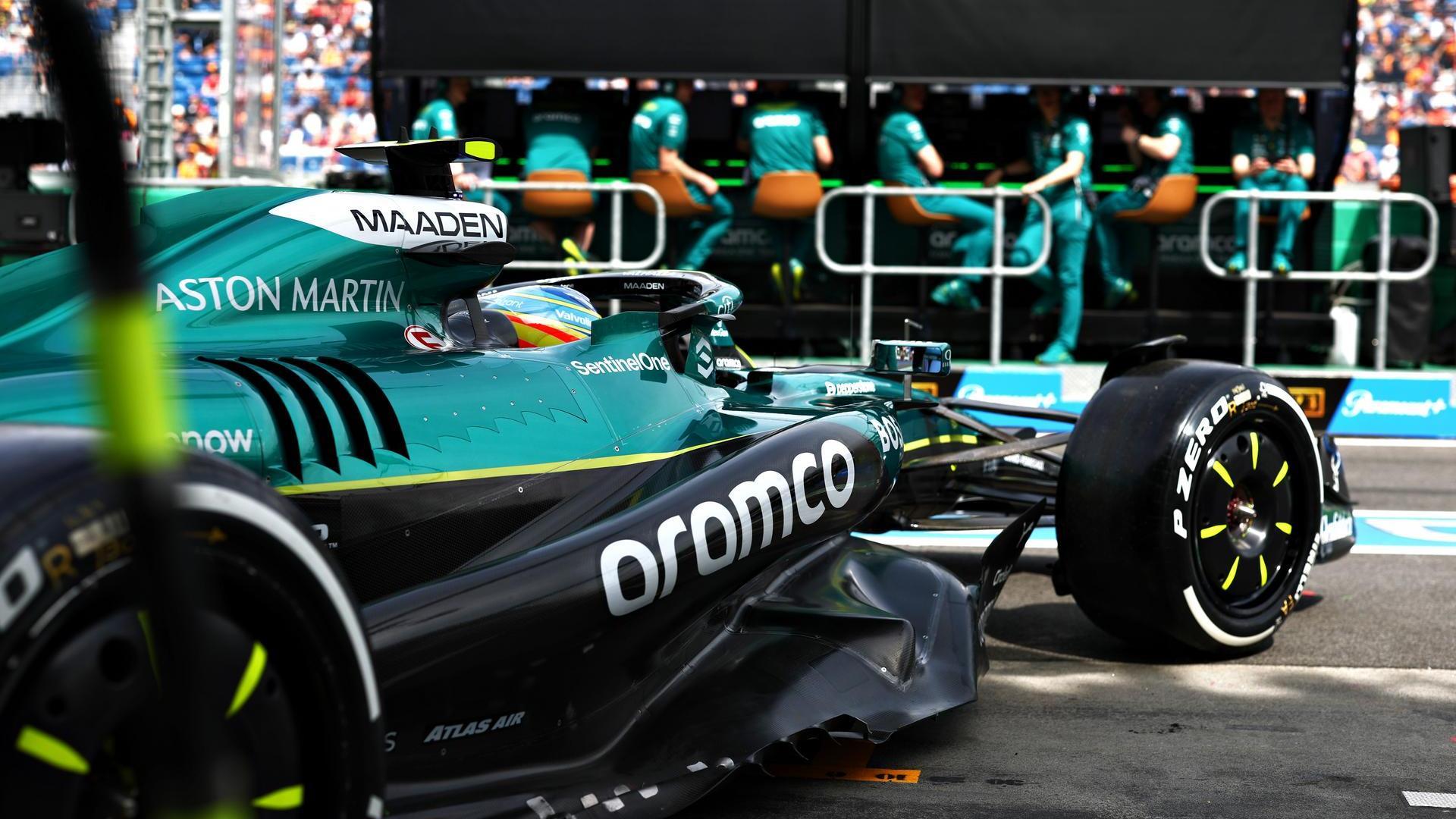
Sign up for a weekly newsletter and we'll make sure you're fully up-to-date in the world of race technology
The first racing cars to feature regenerative brakes were essentially prototypes to evaluate the efficacy of hybrids in motorsport, but advancements in battery technology meant that they would soon become the norm on the road and the racetrack.
The experimental AMC Ambition debuted regenerative braking on the road in 1967 but it was in the Toyota Prius where this technology was commercialised. Currently, the majority of hybrid and electric road cars use this system.
Here’s how regenerative braking revolutionised motorsport powertrains.
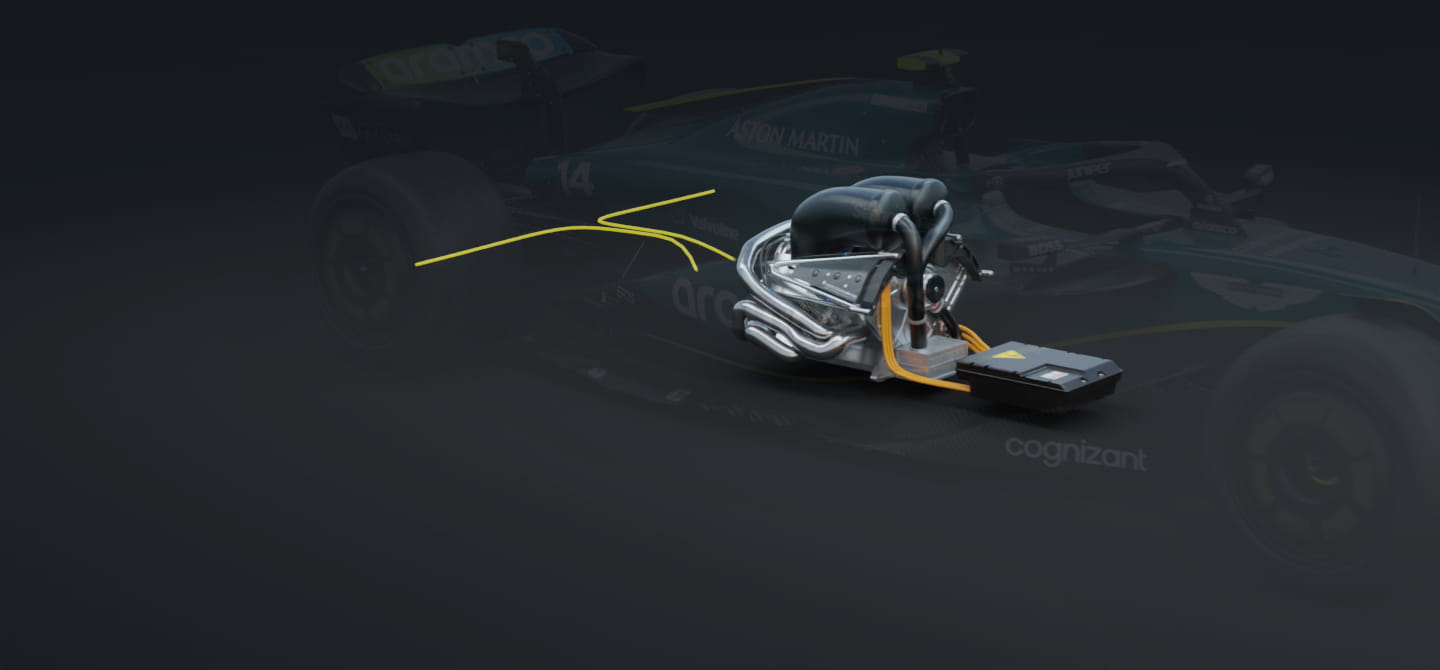
A diagram showing regenerative braking feeding energy back into the battery of the Aston Martin Aramco Formula 1 Team AMR24
What is regenerative braking?
Regenerative braking essentially involves converting the kinetic energy of a car’s motion into electrical energy during braking. That electrical energy can then be temporarily stored in a battery before it is released and ‘regenerated’ back into kinetic energy to power the car.
This process takes place via what is most commonly termed a Motor Generator Unit (MGU), which acts as part of an Energy Recovery System (ERS), although in the early days, the system was termed a Kinetic Energy Recovery System (KERS).
During harvesting of energy, under braking the MGU acts as a generator, transforming the rotational kinetic energy of the engine crankshaft into electrical energy, which is transmitted to the battery (also known as an Energy Store, or ES).
When a power boost is required, the electrical energy stored in the battery can be supplied to the MGU, which then operates as an electric motor, applying additional torque to the engine’s crankshaft, effectively increasing the power.
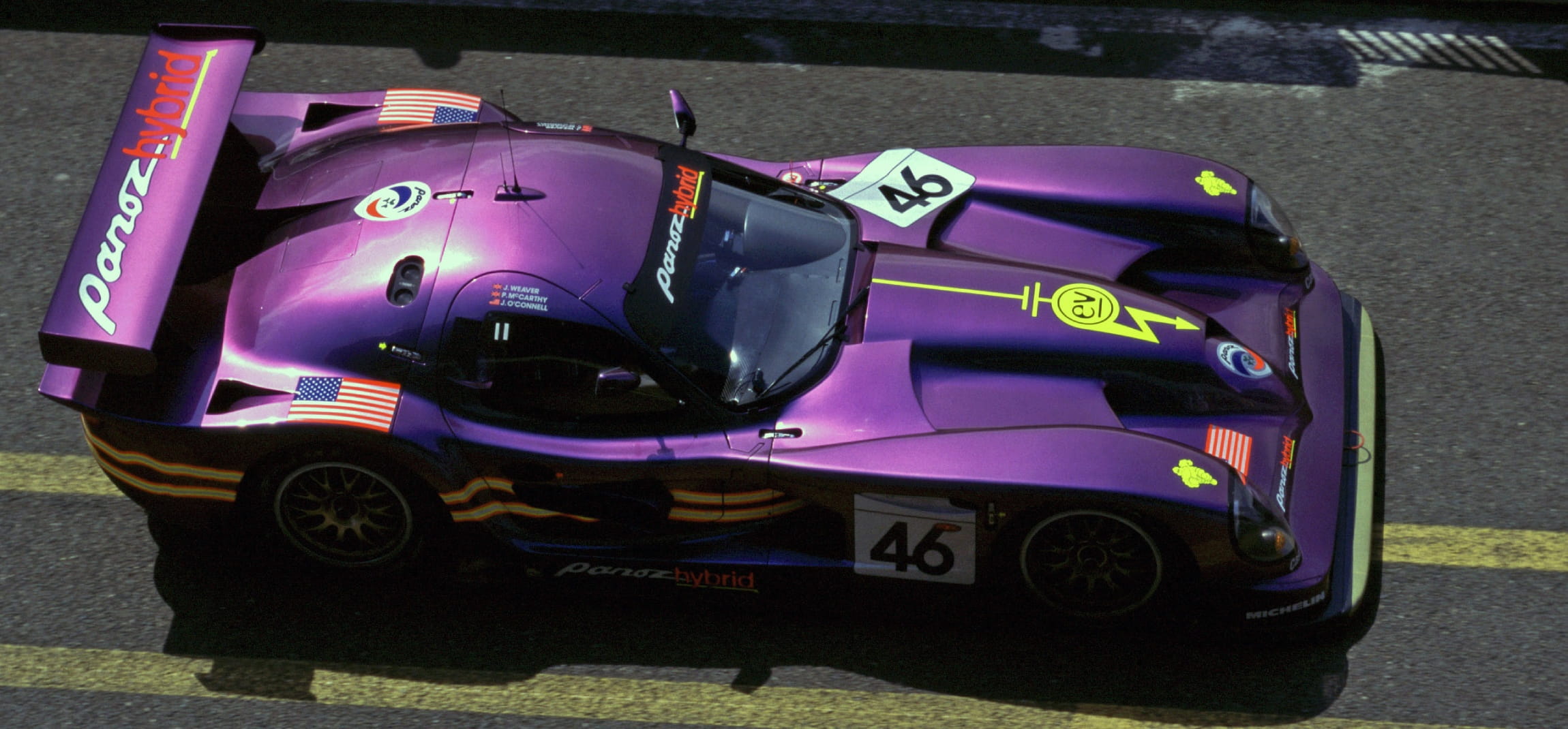
<div>The Panoz Q9 GTR-1 Hybrid pioneered regenerative braking in motorsport when it debuted in 1998. Image courtesy of Robert Dalaudiere<br></div>
The first regenerative braking systems in motorsport
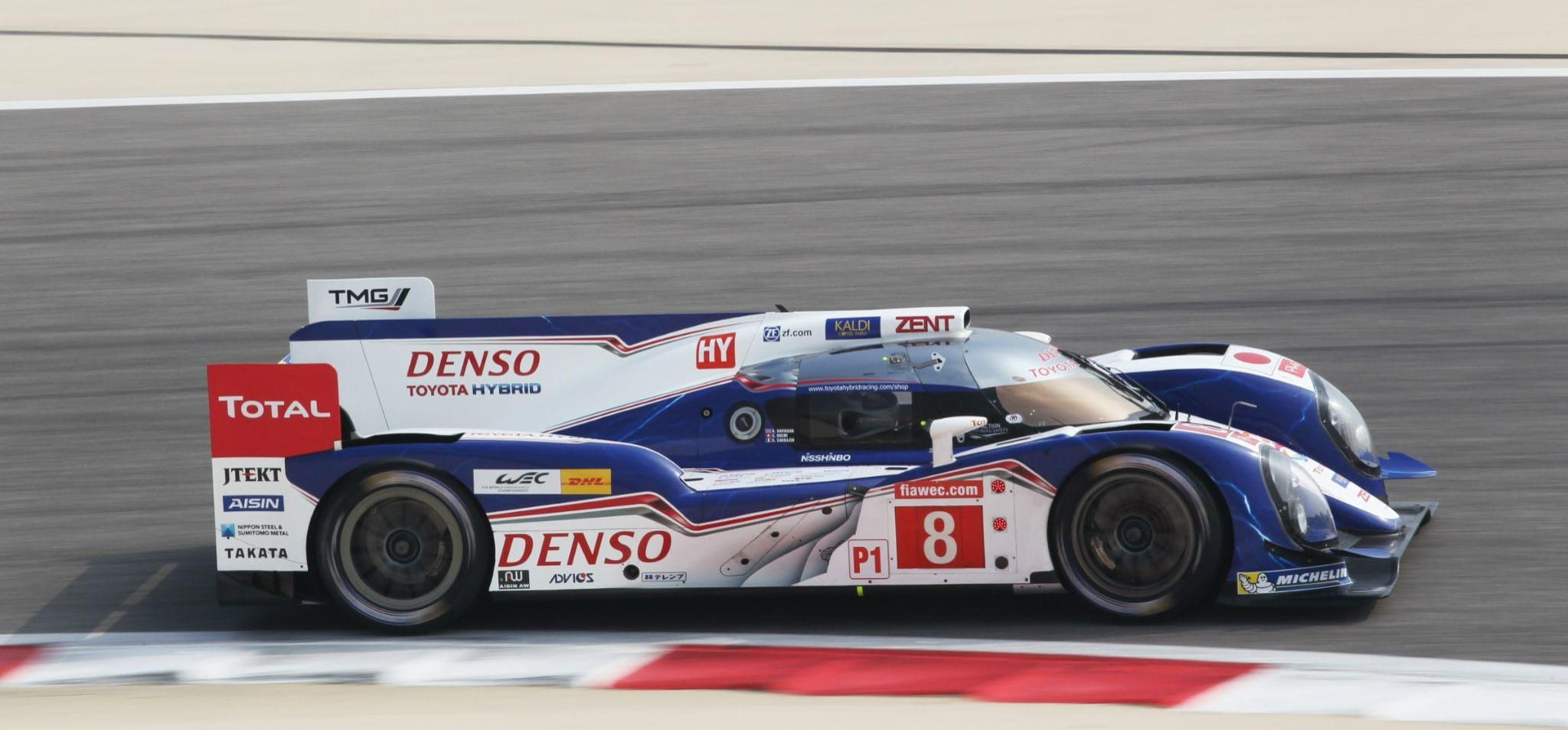
The Toyota TS030 LMP1 car was one of the first hybrid cars to find success in competitive motorsport
KERS in Formula 1
The early days of the Kinetic Energy Recovery System (KERS), which was first introduced to F1 in 2009, saw an MGU which was gear-driven from the front of the engine crankshaft, and recovered energy which, with a fully charged battery, could provide up to 80bhp extra power, available to the driver though the push of a button on the steering wheel. The energy use was regulated via the car’s FIA standard ECU, and could be used for a maximum of 6.67 seconds per lap. The energy-usage strategy was down to the driver, and the additional power could be used in one go, or could be used in several smaller ‘chunks’ during each lap.
This early system was used by most teams primarily to provide an extra power boost on the run to the first corner at the start of a race, though it could also be used to aid overtaking.
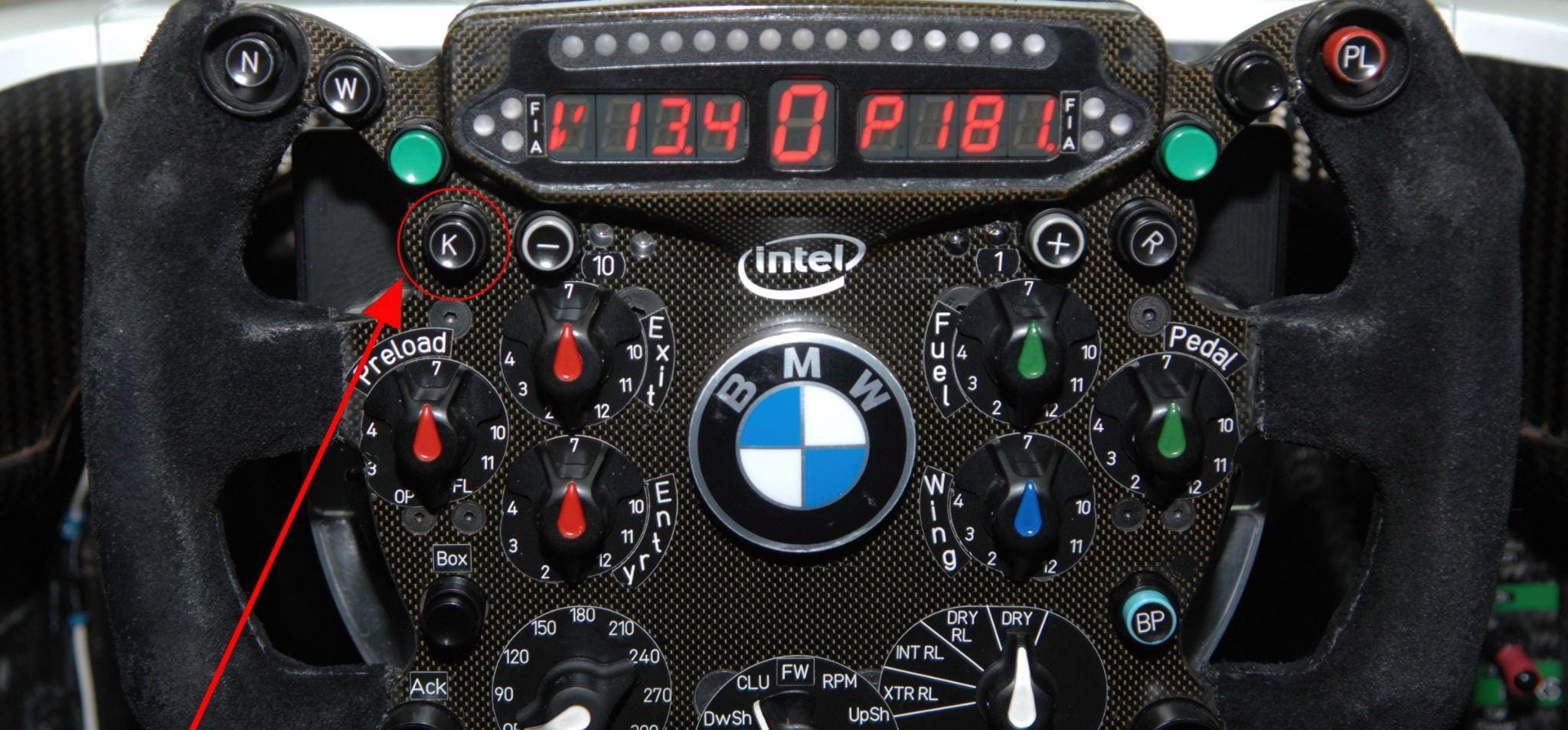
A red arrow showing the KERS button on the steering wheel of the 2008 BMW Sauber F1.08b Formula 1 car, which was used to test for the 2009 F1 season in which KERS debuted
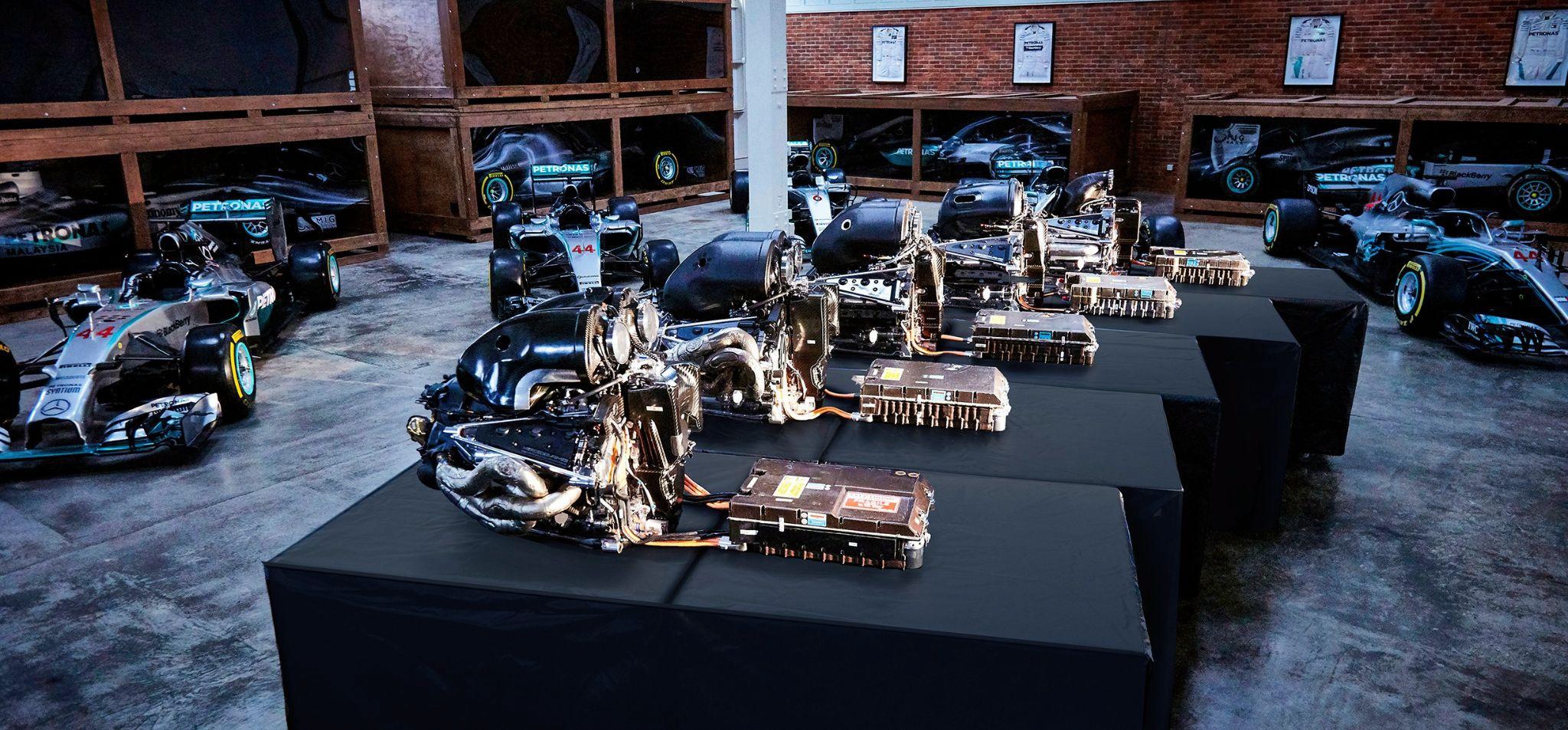
From right to left, a line-up of Mercedes AMG hybrid F1 power units from 2014-2018
Regenerative braking and hybrid use in current F1 cars
The current F1 Technical Regulations, in force until the start of the 2026 season, limit the rotational speed of the MGU-K to 50,000rpm, and the unit’s maximum power output must not exceed 120kW, with a maximum regulated torque of 200Nm. From 2026, the regulation changes will outlaw the use of the MGU-H, which will place more emphasis on the efficiency and operation strategy of the MGU-K.Electronic brake control is necessary for hybrid F1 cars, as there are effectively three forms of braking acting on the rear axle: engine braking provided by the internal combustion engine, braking effect provided by the MGU-K when operating in ‘regen’ mode, plus braking provided by the conventional hydraulic brakes.
As a result, the contribution provided by the hydraulic brakes needs to be adjusted when the MGU-K is recovering energy, as less hydraulic braking effort is required at the rear axle in order to maintain consistent front-to-rear brake bias. Of course, increased hydraulic braking effort is required when the MGU-K is not harvesting energy.
Although the driver can control the sources of braking effort using controls on the steering wheel, a form of automatic control is required to avoid the driver having to make constant adjustments to maintain control of the car. Additionally, the operation of the MGU-K itself needs to be controlled to avoid overcharging the battery.
A ‘brake-by-wire’ electronic control system controls the hydraulic braking effort to provide consistent and predictable braking, avoiding the fluctuations which would otherwise occur when the MGU-K is operating, and hence, importantly, maintaining the driver’s confidence in the handling of the car.
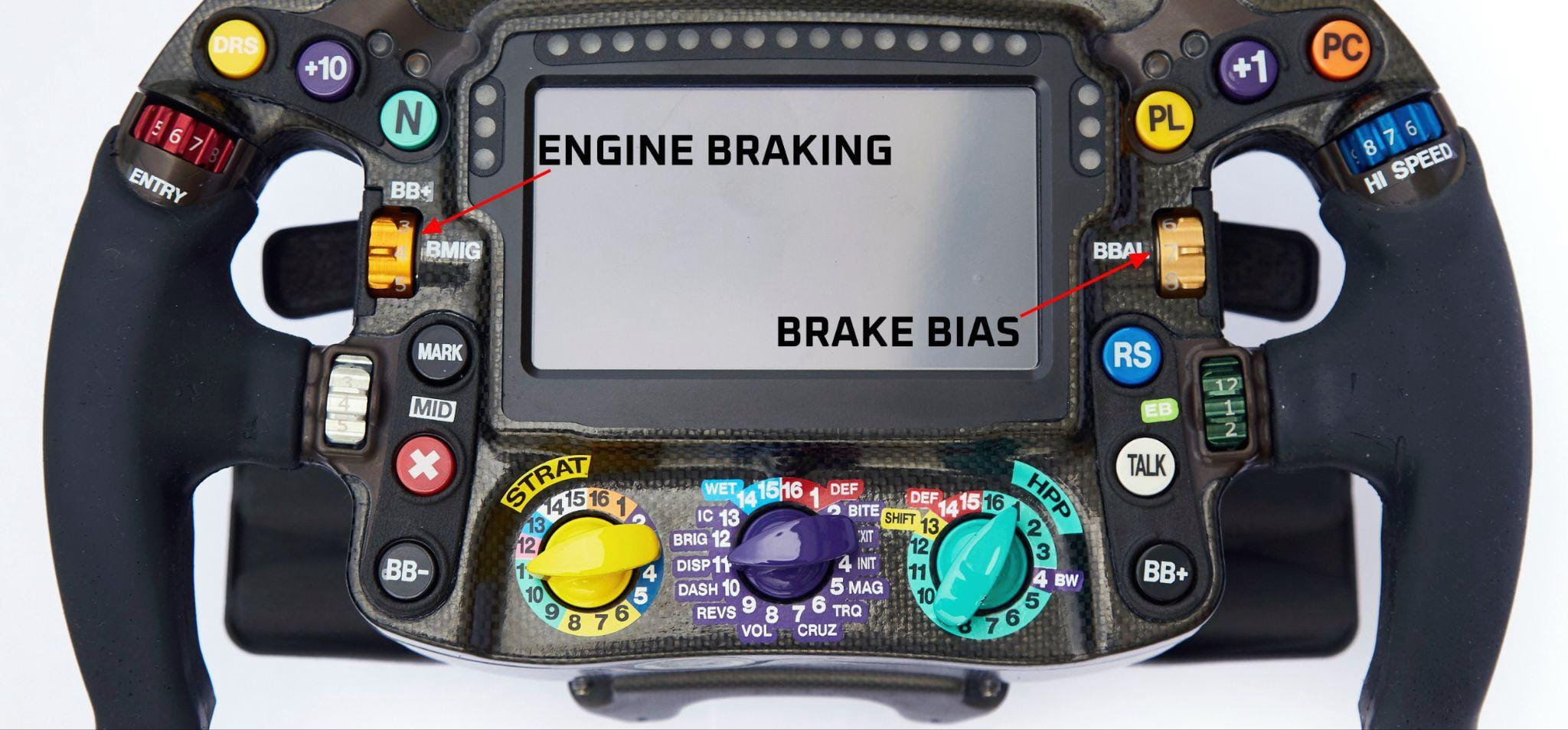
An annotation on a Mercedes F1 steering wheel pointing out the yellow dial used to change the strength of engine braking (L) and the darker yellow dial used to change the brake bias from the front to the rear or vice versa (R)
How regenerative braking is used in fully electric racing
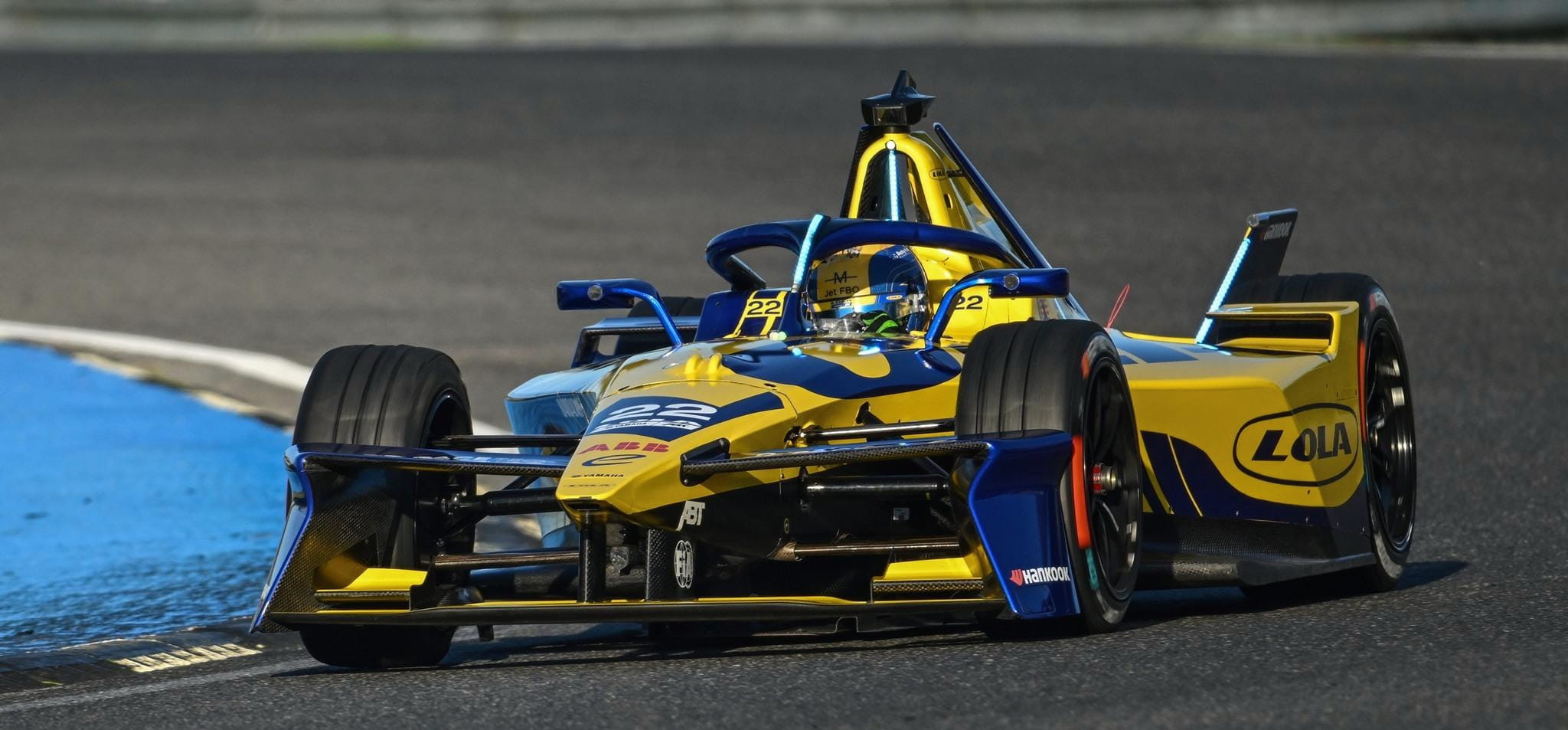
Current Formula E cars use regenerative braking on the front and rear axles while F1 cars only have regeneration on the rear axle