Car
Turbochargers in motorsport: how turbos improve efficiency and power
by Steve Rendle
7min read
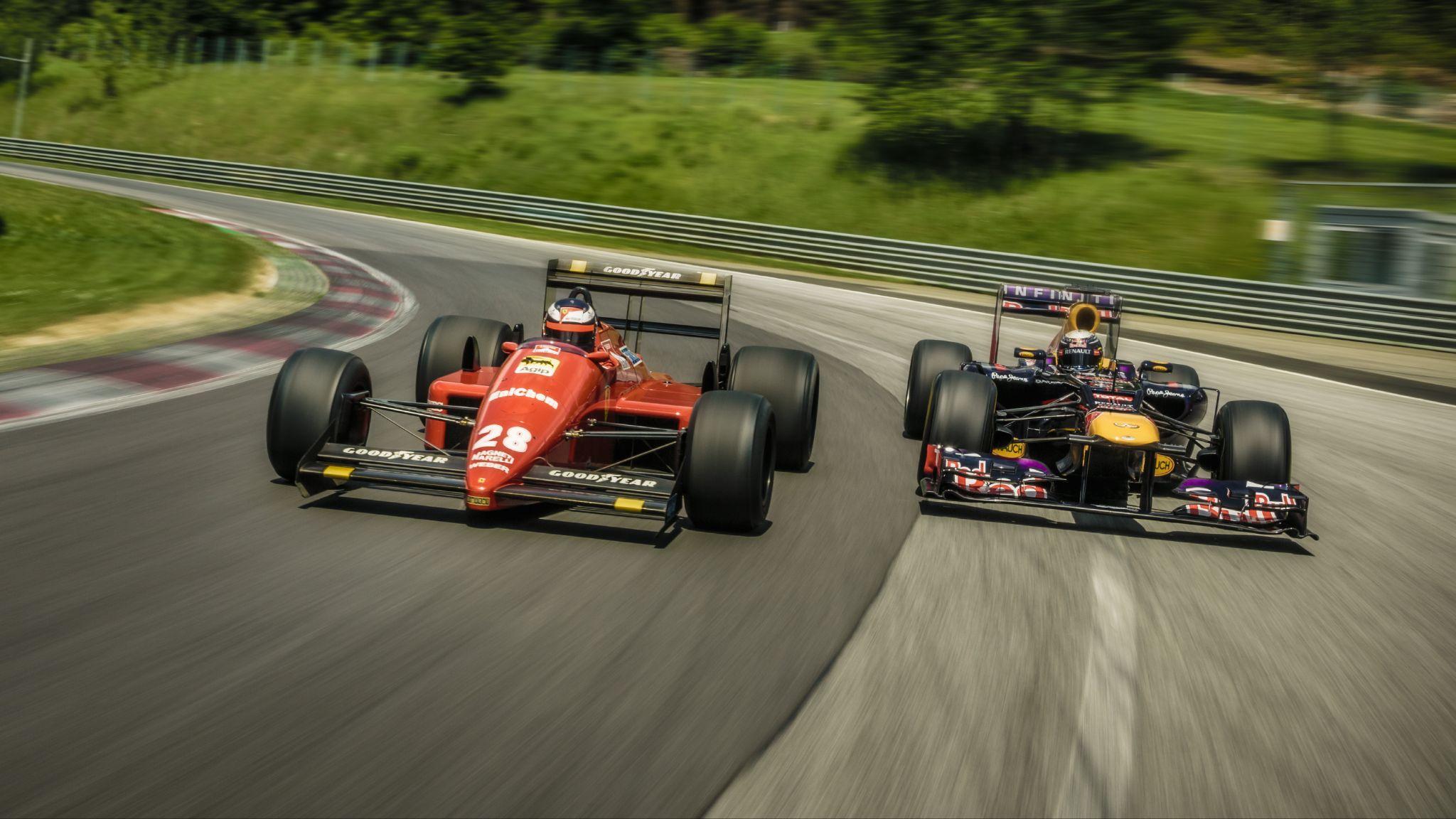
The turbocharged engine has been used in motorsport ever since 1952. How does the turbocharger device enhance efficiency and power - and why is it so commonly used in internal combustion engines?
A turbocharger uses the residual kinetic energy of the exhaust gases expelled by an internal combustion engine to compress the intake air, forcing more air into the engine.
By increasing the quantity of air entering the engine, enabling it to burn more fuel, more power can be produced by the internal combustion engine.
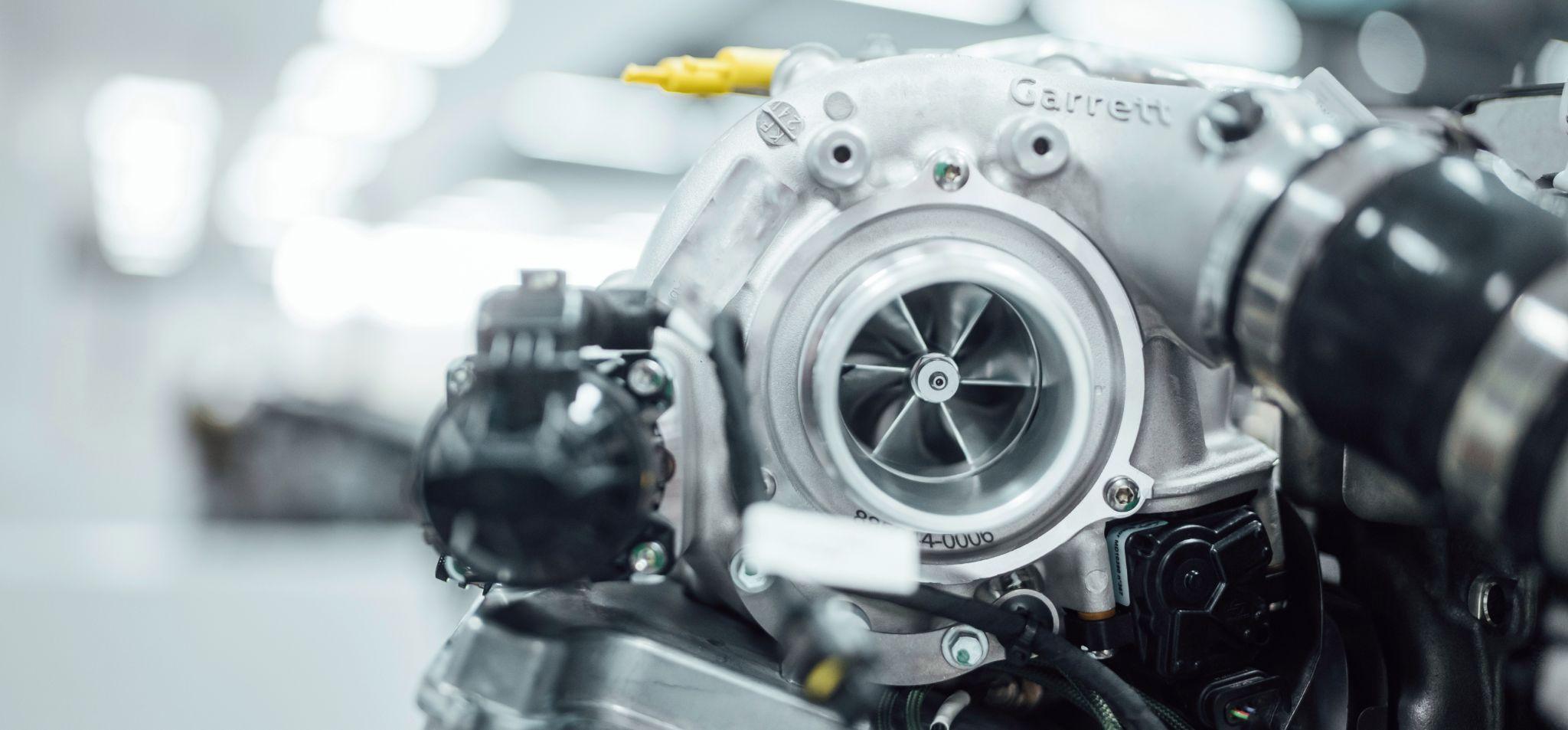
A Garrett turbocharger bolted to an engine, with the turbine in view
The history of turbocharging
Turbocharging differs from supercharging in that turbocharging uses an exhaust-gas-driven compressor, whereas a supercharger uses a compressor driven mechanically from the engine crankshaft.
The serious development of turbochargers began during World War I, to compensate for the significant reduction in power due to the less-dense air when aircraft flew at relatively high altitudes, and turbos were first used with marine and railway locomotive engines in the 1920s - and some truck engines in the 1930s.
In 1952 a turbo-diesel-powered car (the Cummins Diesel Special) took pole for the Indianapolis 500. This car is the first turbocharged car to participate in a major motorsport event.
It was the 1960s before the first turbocharged road-car engines appeared, initially in the United States. By the 1980s the adoption of turbochargers had become widespread, particularly in motorsport where they dominated Formula 1, sportscar racing and rallying by the mid-1980s.
At the 1979 French Grand Prix, Renault won its home race - and the Renault RS10 became the first turbo-powered car to win a Formula 1 grand prix.
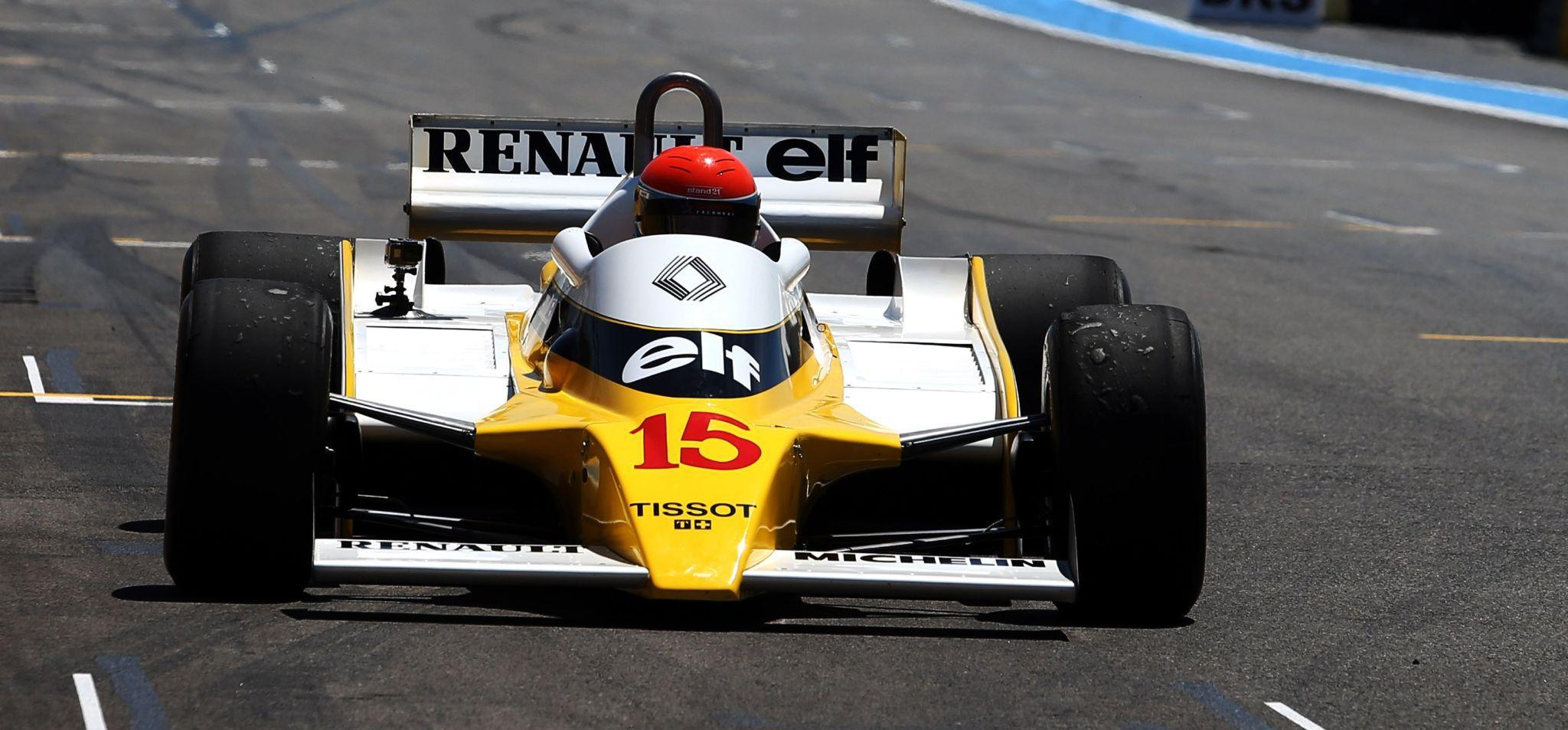
The Renault RS10 is the first turbocharged Formula 1 car to win a world championship grand prix, having done so in the 1979 French Grand Prix
How does a turbocharger work?
In its simplest form, a turbocharger comprises an exhaust-driven turbine, connected via a shaft to a compressor that compresses air before it is fed into the engine intake system.
As the rotational speed of the turbine and compressor varies with exhaust pressure (speeds can reach in excess of 125,000rpm, or 2,083 revs per second), and therefore engine revs, the maximum boost delivered needs to be controlled to avoid engine damage.
This control is provided by a wastegate, which opens to ‘dump’ excess pressure when a predetermined maximum pressure is reached.
The design of the turbine and the compressor is critical. The turbine is designed to be as efficient as possible, to minimise turbulence and to ensure smooth airflow into the engine intake system. An efficient compressor improves throttle response, reducing turbo ‘lag’ (the delay between the driver pressing the throttle and the turbocharger delivering boost).
The turbocharger components are subjected to extremely high temperatures (due to the exhaust gases) and pressures, and must be made from materials that can withstand these harsh conditions.
In the early days of turbocharging, component failures were common.
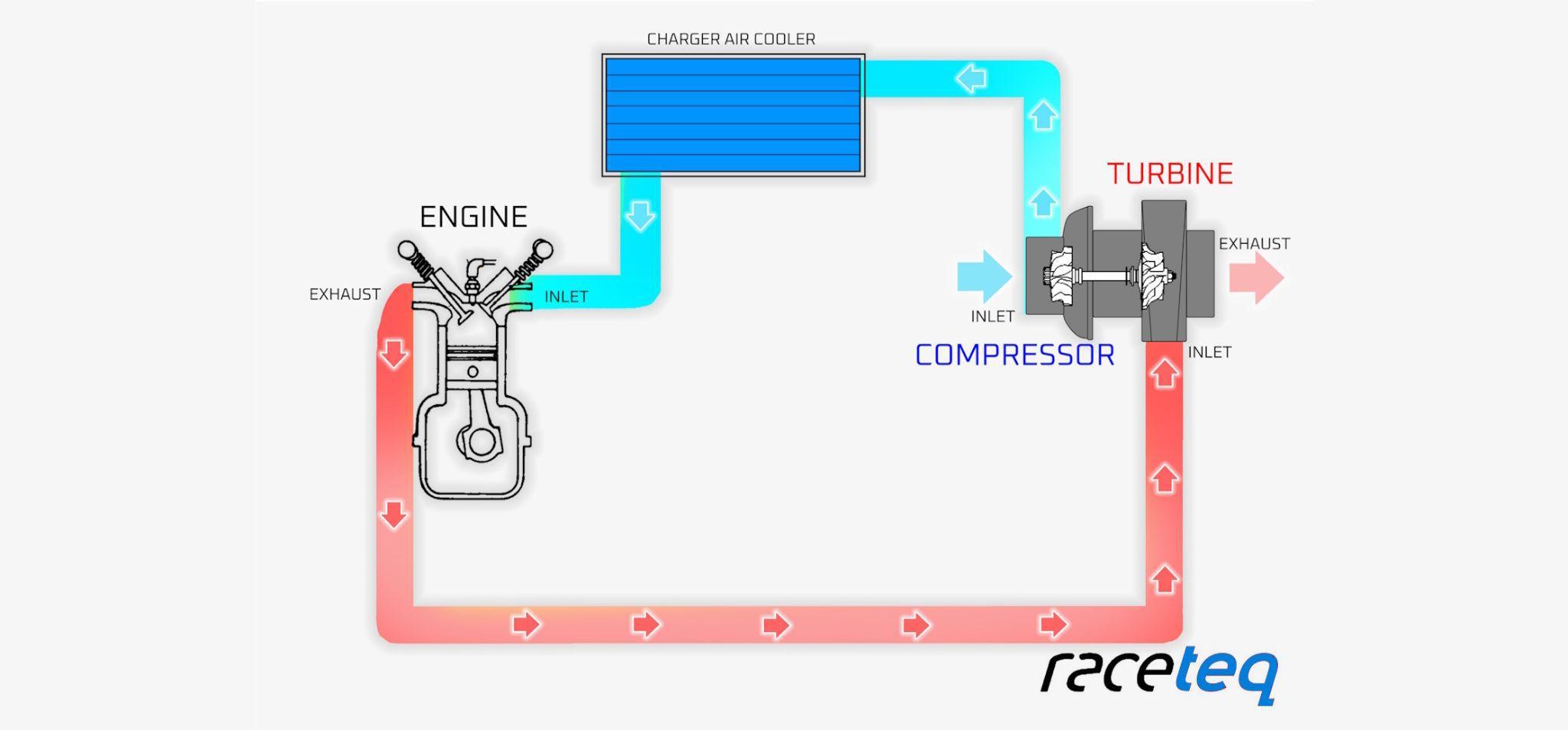
A diagram showing airflow within a turbocharged system with gases going from the engine to the turbocharger before they are cooled and returned to the engine
Ensuring the safety and efficiency of turbos
The turbocharger shaft bearings and their lubrication system are critical. The bearings must control the movement of the shaft, allow for vibration, and must minimise frictional losses. In order to contain the lubricating oil within the shaft/bearing area of the turbocharger housing, robust seals are required.
An intercooling system is used to reduce the high temperature of the compressed intake air before it enters the engine.
The higher the temperature of the intake air, the lower its density, and the lower the oxygen content, reducing the efficiency of the combustion process, and hence the effectiveness of the turbocharging.
Air-to-air intercooling is generally used, which routes the compressed intake air through a large radiator.
Turbocharger technology has evolved significantly in recent years, and the majority of petrol road-car engines are now turbocharged, with constant evolution of the turbo systems used in motorsport.
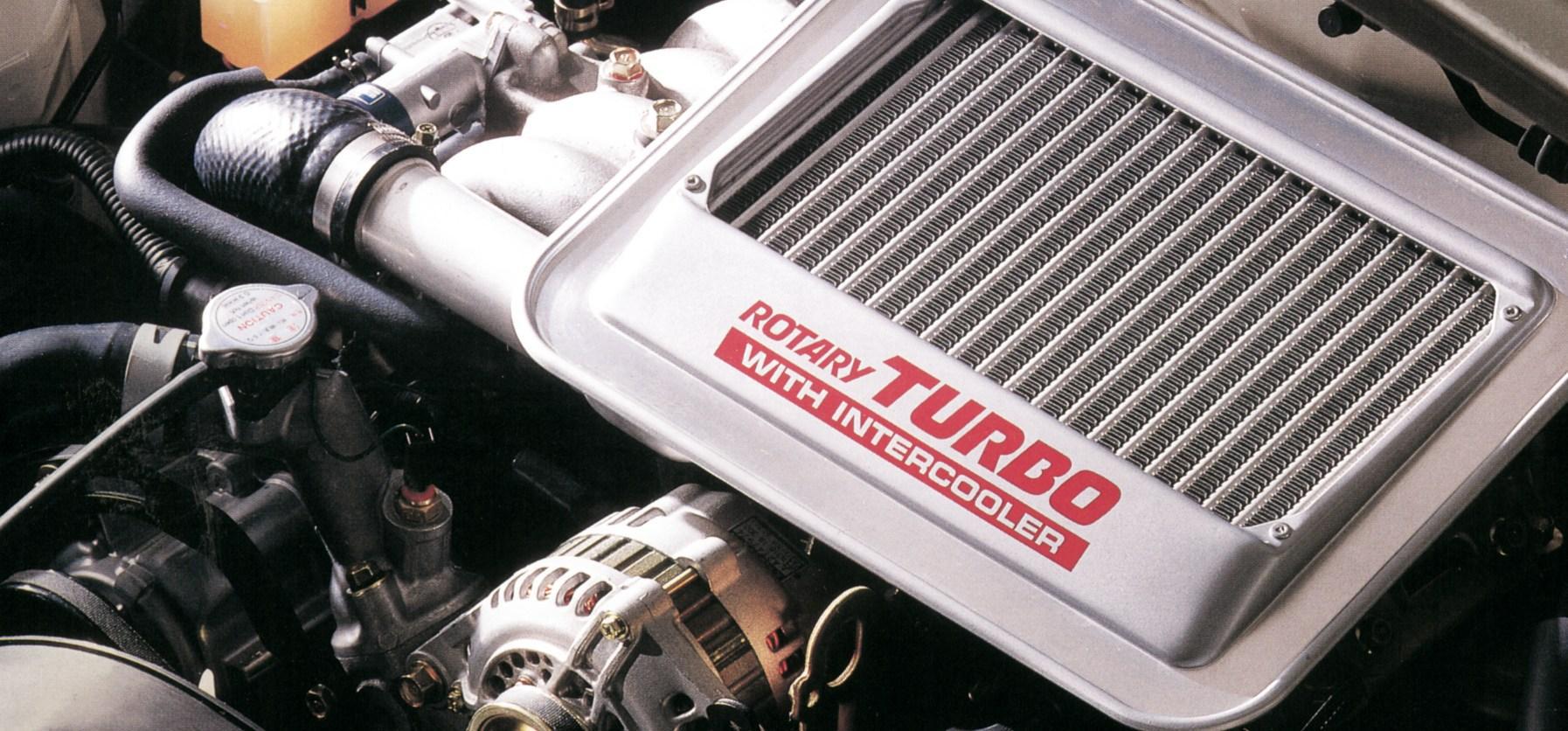
An image of the intercooler - essentially a heat exchanger - in the Mazda RX-7
How different types of turbos work
With a conventional turbocharger – known as a constant-pressure, or single-scroll turbocharger – the exhaust gas from all the engine cylinders flows to the turbine via a single duct (known as a ‘scroll’).
As the exhaust pulses from each cylinder tend to interact and dampen each other out in the exhaust manifold before entering the turbocharger, the overall exhaust pressure is reasonably constant, hence the term ‘constant pressure’.
However, with a single-scroll turbocharger engine performance can be relatively poor at low and medium engine speeds and loads, and the engine can suffer from turbo lag when accelerating.
A twin-scroll turbocharger is often used on four- and six-cylinder engines, splitting the flow of exhaust gases from the engine exhaust ports to the turbocharger into two separate paths (twin scrolls), minimising interference between the exhaust pulses.
Because the scrolls are separated, the two exhaust flows can be directed to the turbine vanes independently. The exhaust gas pressure can be controlled according to the diameter of the scrolls, so higher-pressure air supplied through a smaller-diameter scroll can be directed to the inner ends of the turbine blades, and lower-pressure air supplied through a larger-diameter scroll can be directed to the outer ends of the blades.
This enables the turbine speed to be increased (compared to a single-scroll turbo) at lower revs, reducing lag and improving throttle response, providing a more even power band.
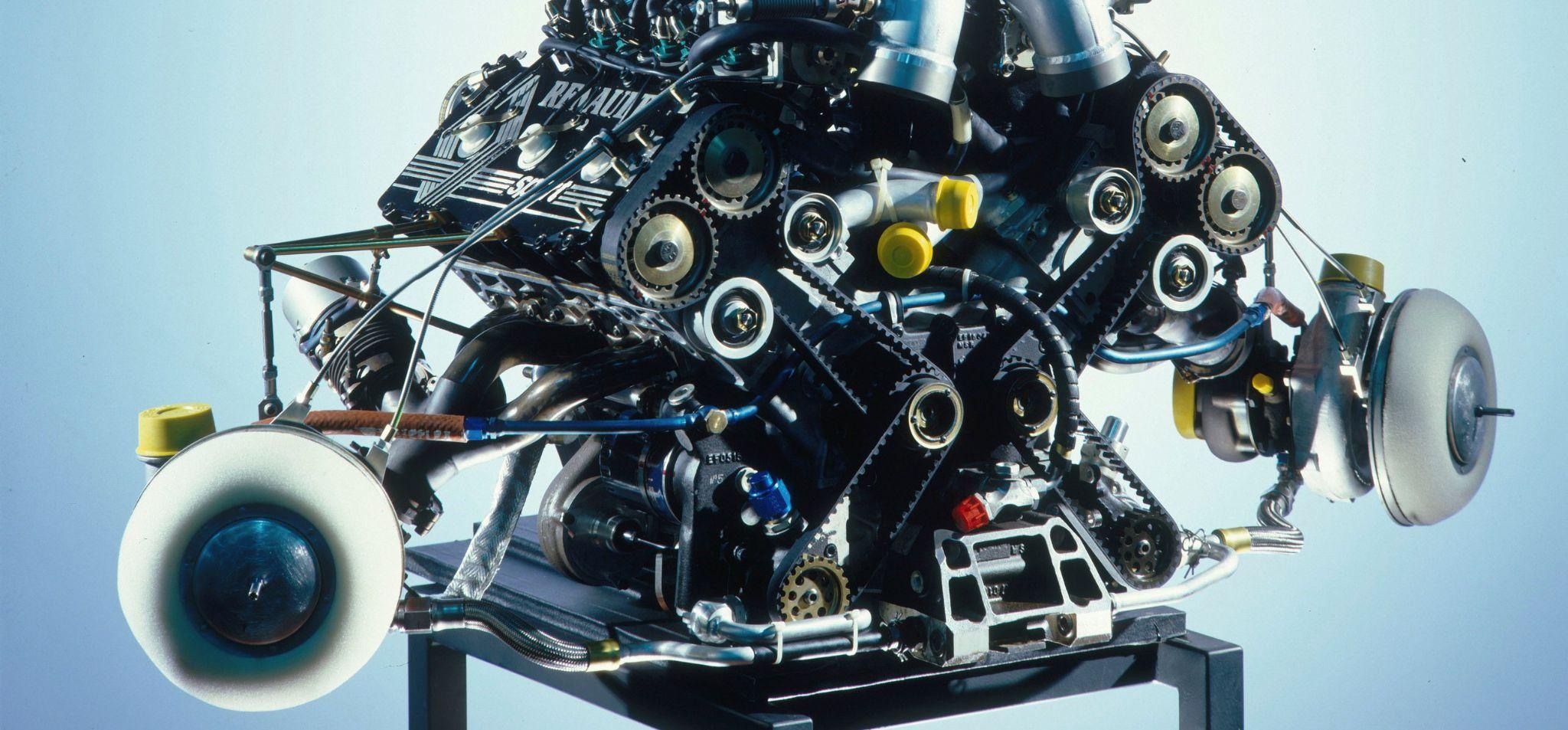
A photograph of a twin-turbo V6 Renault EF15 Formula 1 engine that was introduced by the team from 1979 - and brought it considerable success
This arrangement reduces turbo-lag by using two smaller turbos – one for each cylinder bank – and was commonly used with the V6 turbo engines seen during the first F1 turbo era during the 1980s.
A variation on the twin-turbo configuration is the sequential turbocharging system, as used on the Porsche 959 in the late 1980s.
This system reduces turbo lag by allowing a smaller turbo to work at lower engine revs, and then as engine revs rise, a controlled amount of exhaust gas is fed to a larger turbo, enabling it to ‘spin up’ before all the exhaust gas is directed to the larger turbo, providing increased boost at higher engine revs.
Variable-geometry turbochargers have also been used in motorsport in recent years, although because the components are susceptible to failure with the very high exhaust-gas temperatures produced by petrol engines, these systems are more common on diesel engines.
Variable-geometry turbochargers work by controlling airflow through the turbine using a sequence of vanes that allow for more or less airflow depending on how much air the engine needs. The vanes open at high speeds to feed more air into the engine and maintain the required boost pressure.
However, Porsche pioneered a variable-geometry turbo system for use on its 997 Turbo road car, and a variable geometry compressor is used on the current-generation hybrid F1 engines (the FIA regulations do not allow this for the turbine).
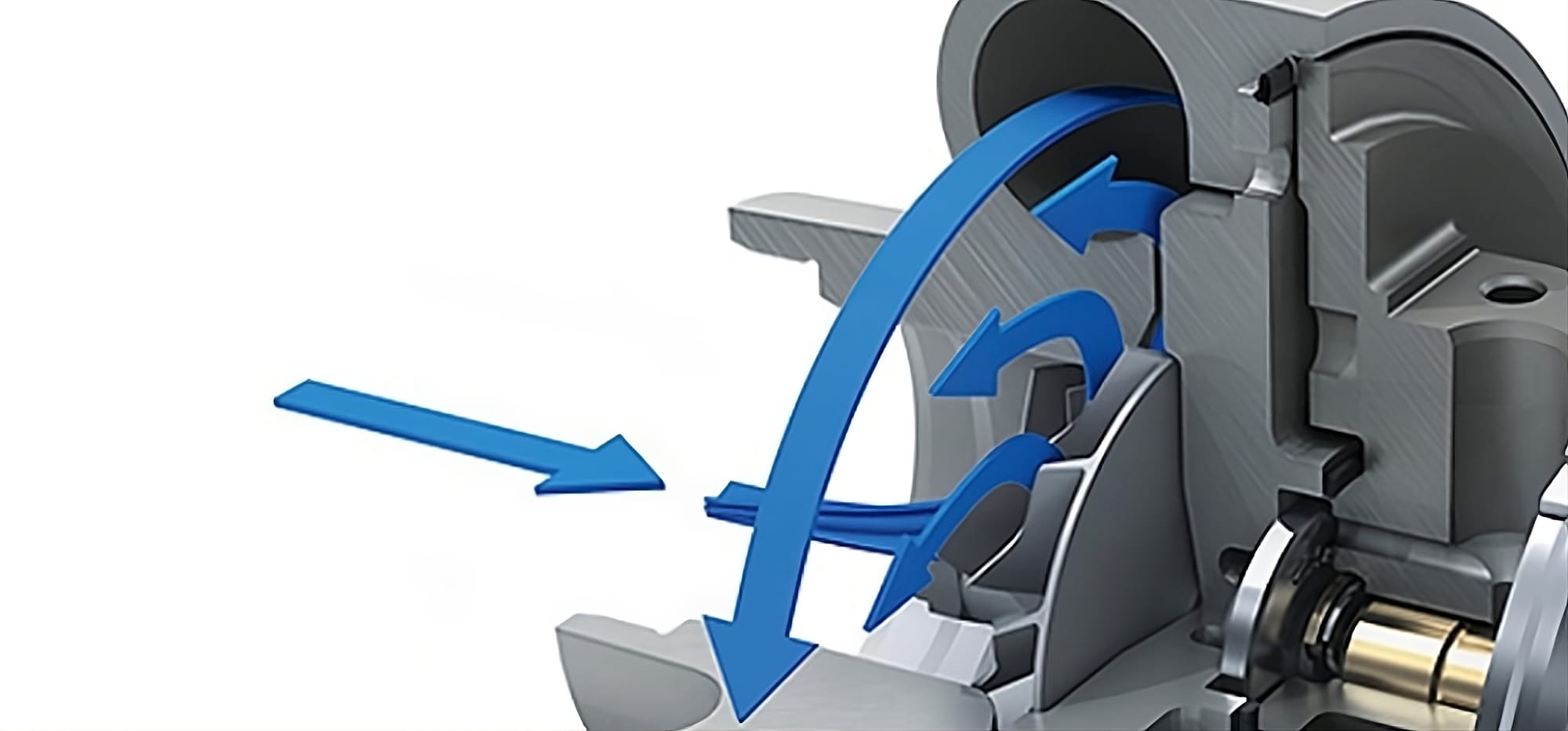
A diagram showing airflow through a variable-geometry turbocharger with the air flowing through various vanes before it reaches the turbine, courtesy of Porsche
What is the anti-lag system in turbo engines?
In order to reduce turbo lag, many competition cars – in particular rally cars – are fitted with an anti-lag system. These systems vary in detail, but usually work using engine management strategy to retard the ignition timing, causing the air/fuel mixture to ignite later than usual, producing additional hot exhaust gases.
A throttle bypass system is also often used, which holds the throttle partially open during overrun conditions, maintaining exhaust gas pressure and therefore keeping the turbo spinning.
Some systems also inject extra fuel directly into the exhaust manifold, which ignites, increasing exhaust-gas pressure to maintain the speed of the turbo. Anti-lag systems also improve throttle response.
In modern Formula 1 cars, stored electrical energy is used to spin the compressor - a turbine - to ensure immediate boost.
The Motor Generator Unit-Heat (MGU-H) harnesses excess exhaust gases and converts this to electrical energy, which can be used to spin the compressor for immediate boost (as mentioned) or sent to a battery for use later on.
If deployed, the electrical energy from the MGU-H can boost engine power by up to 10%. In 2026, however, the MGU-H will no longer be used in Formula 1 as part of the new technical regulations.
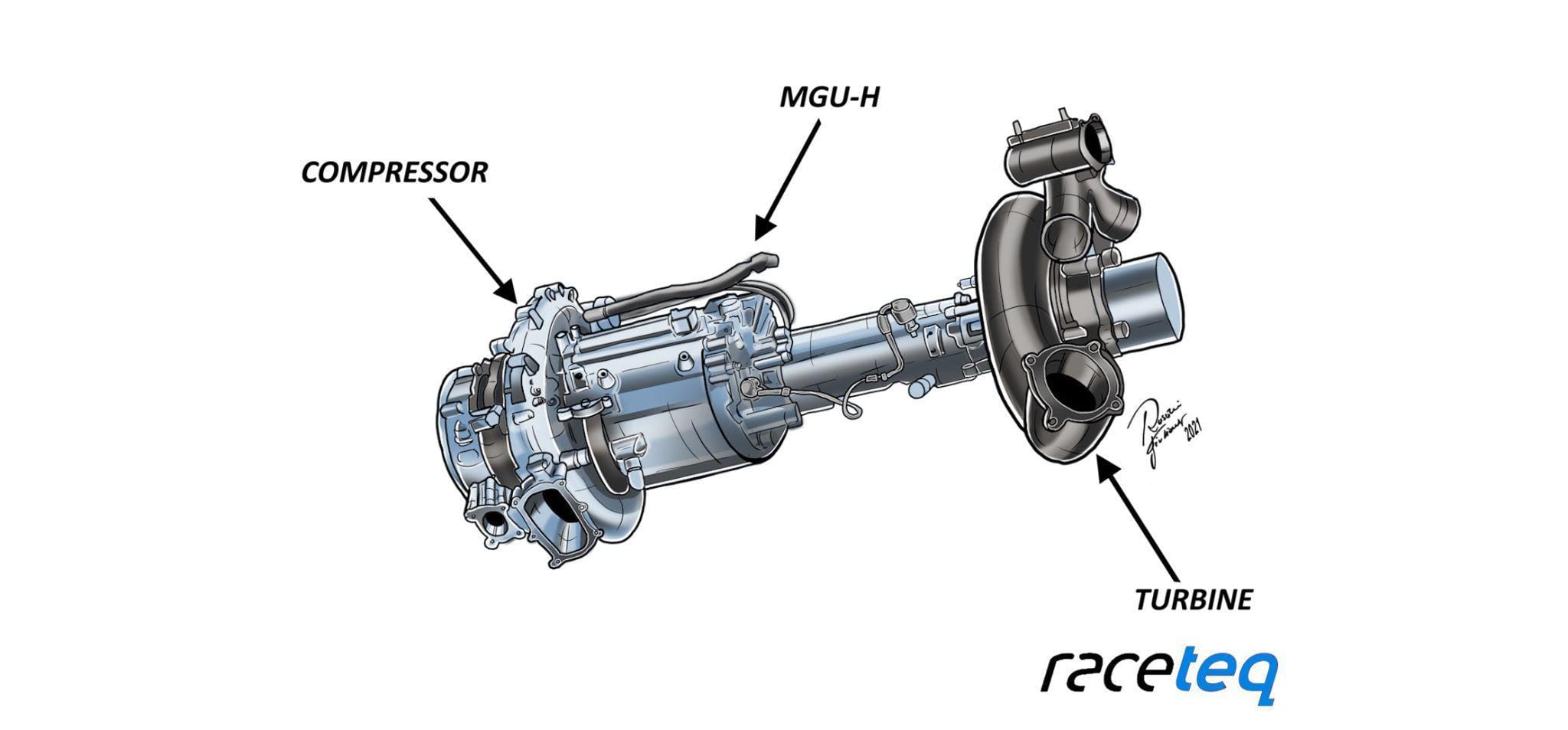
A diagram showing the location of an MGU-H on the turboshaft of a modern Formula 1 engine
The advantages of turbocharging in modern motorsport are numerous: increased power for a given engine size, improved efficiency and improved fuel economy.
Thanks to constant development, the advantages now outweigh the disadvantages: turbo lag and a sudden increase in power, the requirement for a turbo lubrication system, and packaging considerations.
Used in Formula 1, Formula 2, IndyCar, sportscar racing, endurance racing, drifting, the Dakar Rally, and many more disciplines, turbochargers will likely continue to be a feature of internal combustion engines in motorsport - thanks to their efficiency and performance.