Car
CFD in F1: How does Computational Fluid Dynamics drive performance?
by Rosario Giuliana
6min read
.png?cx=0.5&cy=0.5)
Computational Fluid Dynamics (CFD) is an indispensable simulation tool for motorsport teams and manufacturers around the world - but how does it work, and how does it help enhance performance?
Formula 1 teams are constantly in the hunt for engineers who can use and analyse the results of CFD effectively, a technology that is used by motorsport teams in numerous other disciplines - and even in other industries such as construction, air conditioning, and battery design.
So, why do motorsport manufacturers rely on CFD so heavily?
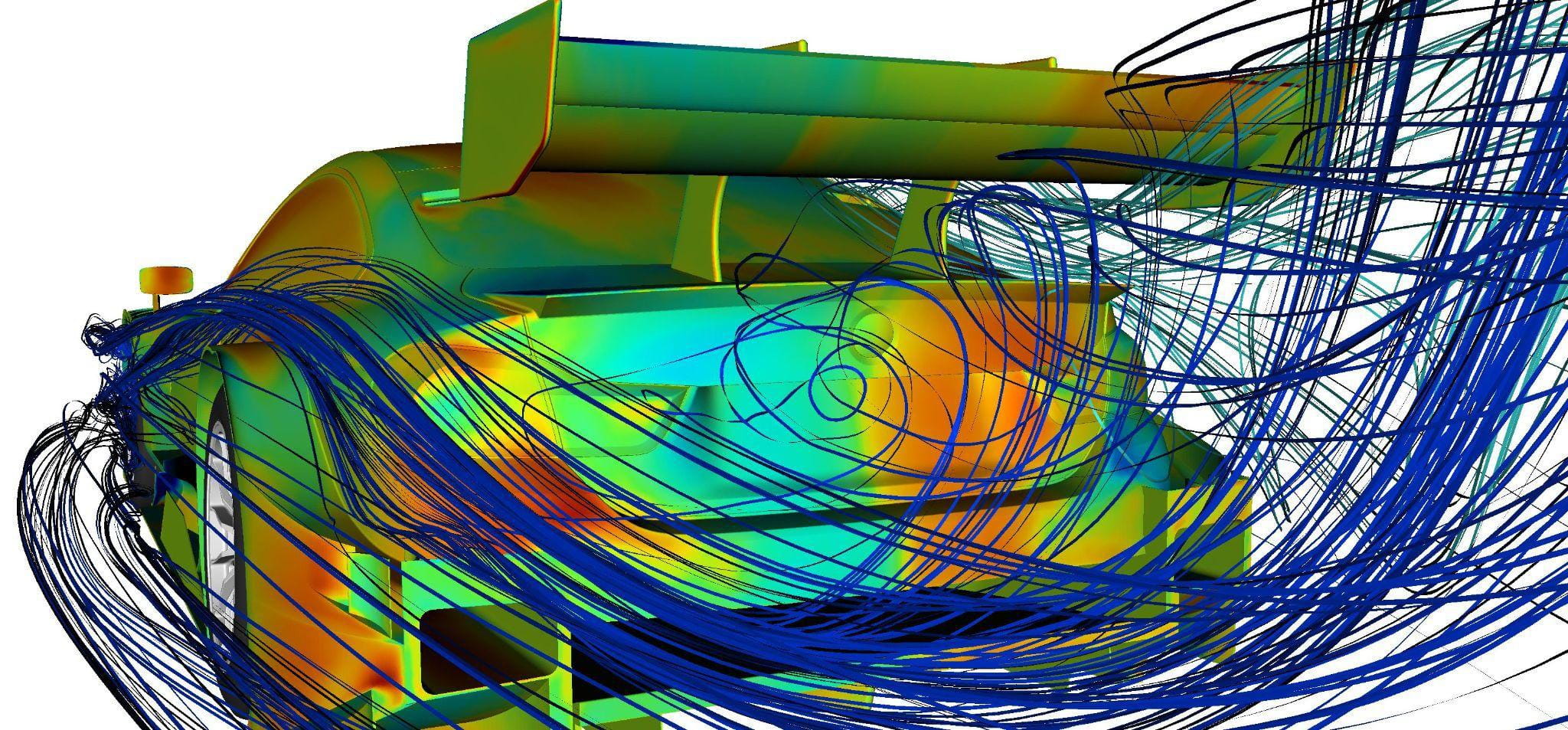
CFD simulation around a BMW M4 DTM touring car showing airflow around the sides of the car and through the diffuser at the rear. Image courtesy of BMW.
What is CFD?
CFD is a branch of engineering that employs powerful software to simulate the behaviour of fluids (like air) around solid objects (such as a wing or bodywork), allowing for the creation of extremely detailed virtual models and their analyses on a computer.
How does CFD work in F1?
With F1 regulations increasingly limiting on-track testing and technological advancements, virtual simulations have become increasingly important for an F1 team. In fact, CFD is arguably the most important tool in the aerodynamic development of an F1 car today.
Through CFD, it is possible to:
- Simulate the airflow around the car, obtaining data such as air velocity, pressure, and temperature at every point in the virtual model.
- Analyse the generation of downforce, allowing visualisation of the areas of the car that generate the most downforce and consequently optimising their shape.
- Reduce drag, visualising the areas that create the most resistance.
- Evaluate the effect of different configurations. Engineers can test virtually different aerodynamic configurations of the car, such as front and rear wings with different inclinations, and choose the one that offers the best compromise for the desired outcome.

An engineer looking at a CFD model of a Formula 1 car
History of CFD: when it was adopted and its early uses
The origins of CFD in the study of fluid dynamics can be traced back to when the first computers began to be used to solve complex differential equations.
However, it is in recent decades that CFD has undergone exponential development, thanks to the increase in computing power of computers and the continued refinement of algorithms.
PHOENICS is the first commercially-available CFD software that was launched in 1981.
As aerodynamics became more important in F1, especially when the first ground-effect cars began to be seen in the late 1970s, and even more so in the 1980s, there was a more inclusive approach by teams toward this technology as they strived to understand ground effect.
During this period, Formula 1 teams began experimenting with the first CFD software to analyse the aerodynamics of their cars.
Initial investment was muted, but it has increased exponentially since the 2000s.
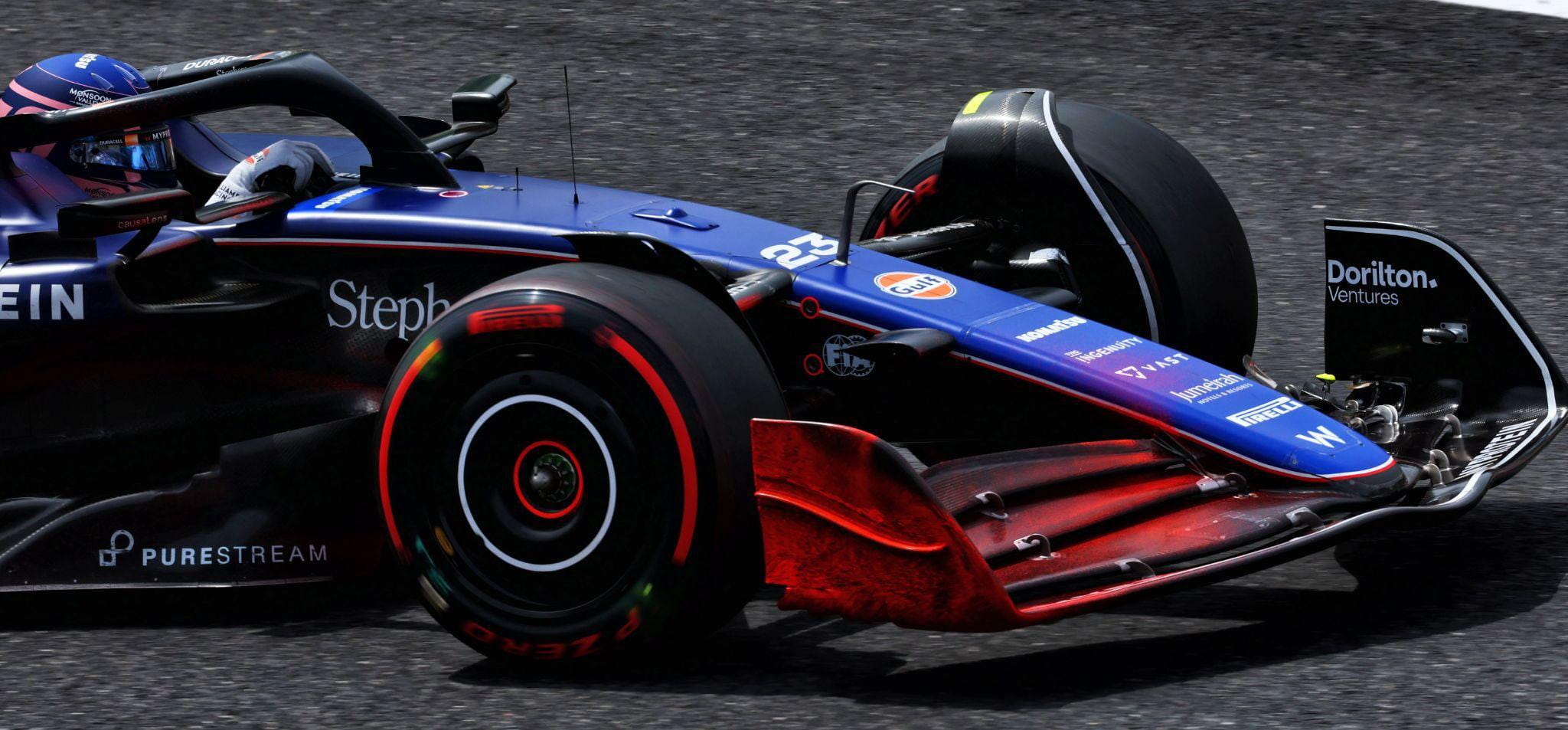
Williams’s Alex Albon driving with flow visualisation - or flow-vis - paint on his car. This paint is used to visualise airflow in a real-life setting
Why CFD has become so important in modern F1
- Regulation reasons: CFD has found wide use in F1 for several factors. One of the main reasons has to do with the FIA's limitations on track test sessions and the use of the windtunnel as per the sporting regulations. Therefore, data collection from the track and windtunnel is becoming increasingly marginal and the main aerodynamic experiments are done on computers with powerful software, which are increasingly being developed to be as close to reality as possible.
- Cost-saving: CFD use is far cheaper than both on-track testing sessions and the energy-intensive windtunnel.
- Time-saving: CFD simulations are relatively quick to generate but teams must abide by the sporting regulations - which limit CFD use by the number of hours spent using cores of the Central Processor Unit (CPU). Instead of producing new parts, teams can design them using CAD (Computer-Aided Design) software and simulate flow behaviour using CFD instead of fabricating parts, putting them on a scale model in the windtunnel, and testing them.
F1 is moving further towards the use of virtual tools and CFD is central to producing a racecar. Furthermore, teams are constantly upgrading their simulation tools to ensure they better reflect what happens on the track
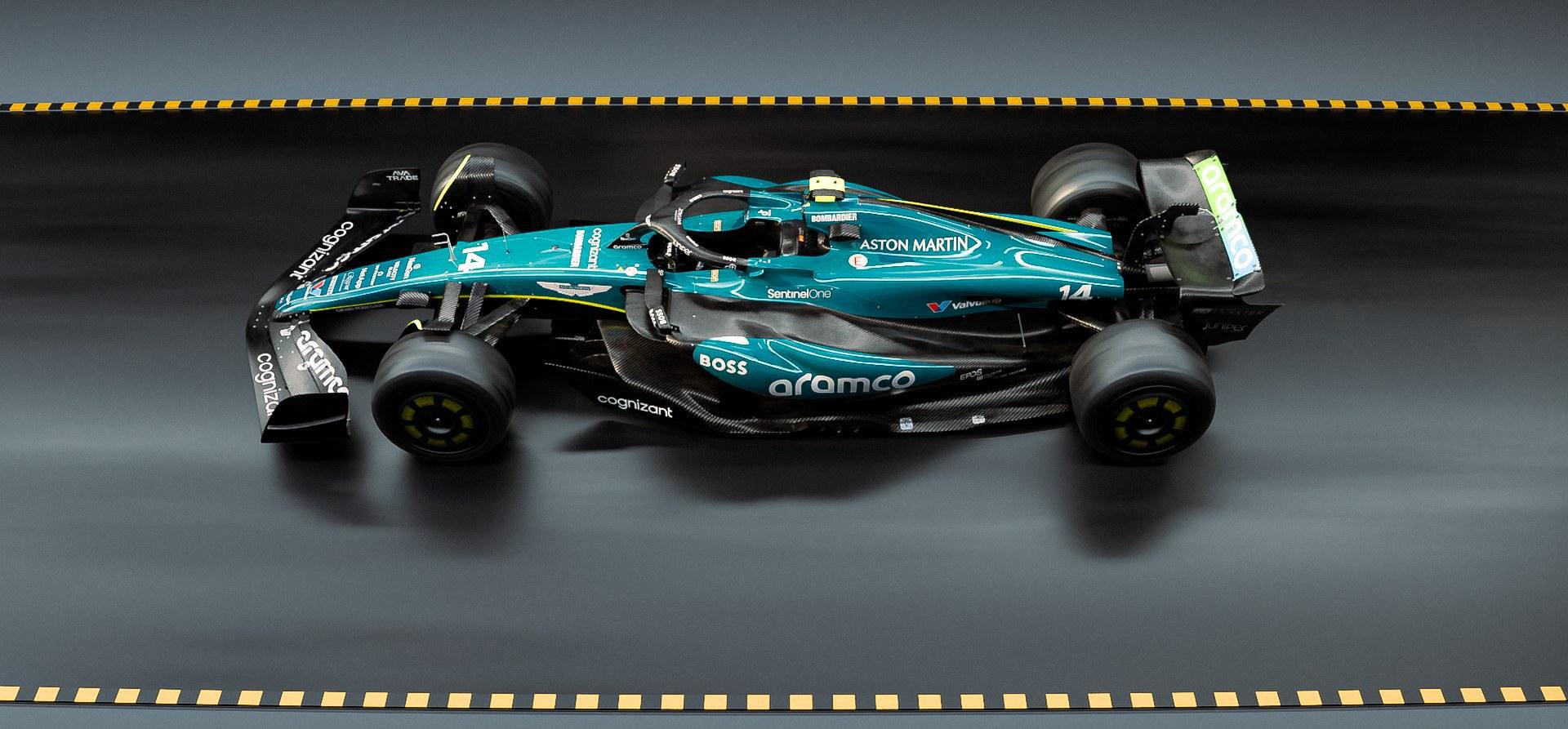
3D render of an Aston Martin AMR24 F1 car in a wind tunnel.
How CFD works with windtunnels and on-track testing
CFD is fundamental to overall performance, but it’s one of many tools that teams can deploy in the chase for better laptimes.
Windtunnels allow teams to test new components with the final materials that they plan to use, obtaining results that are more representative of reality.
However, teams are of course limited regarding how much time they can spend using the windtunnel by the Formula 1 sporting regulations, and running a windtunnel is an energy-intensive and expensive process.
As a result, CFD tends to be the first port of call in aerodynamic development.
If data from CFD shows positive results, the component in question will therefore be developed to verify its benefits in a windtunnel. If the windtunnel confirms the component’s effectiveness, it might be produced and fitted to the car.
That said, the positive and desired behaviour might not fully replicate itself on the track. And when there’s a difference between the positive findings in the factory and the findings on the circuit, teams might cite a ‘correlation’ issue as the reason as to why they have not been able to make a particular upgrade work.
A correlation problem will not only send teams back to the drawing board, but it might also have engineers questioning whether their windtunnel and CFD tools are reliable enough.
This underlines the fact that, while CFD and windtunnels are very useful tools, neither of them can fully replicate what happens on track - and that’s why on-track running remains the most important tool teams have to measure performance.