Car
Motorsport aerodynamics explained: the role of wings, stalling and diffusers
by Steve Rendle
5min read
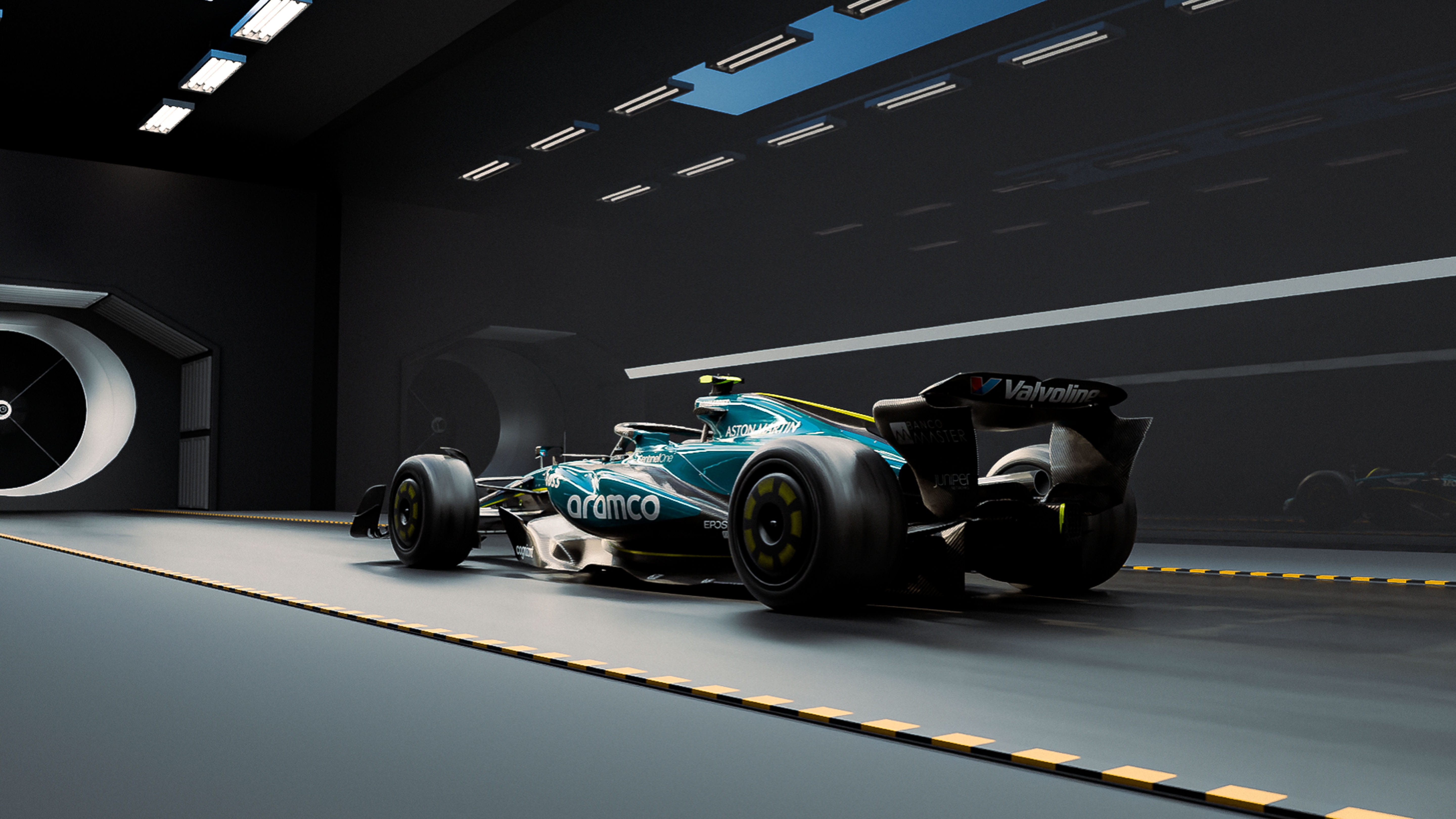
The subject of aerodynamics was first taken seriously as a significant factor in racing car performance during the 1960s - although ‘streamlined’ car designs had been used prior to that.
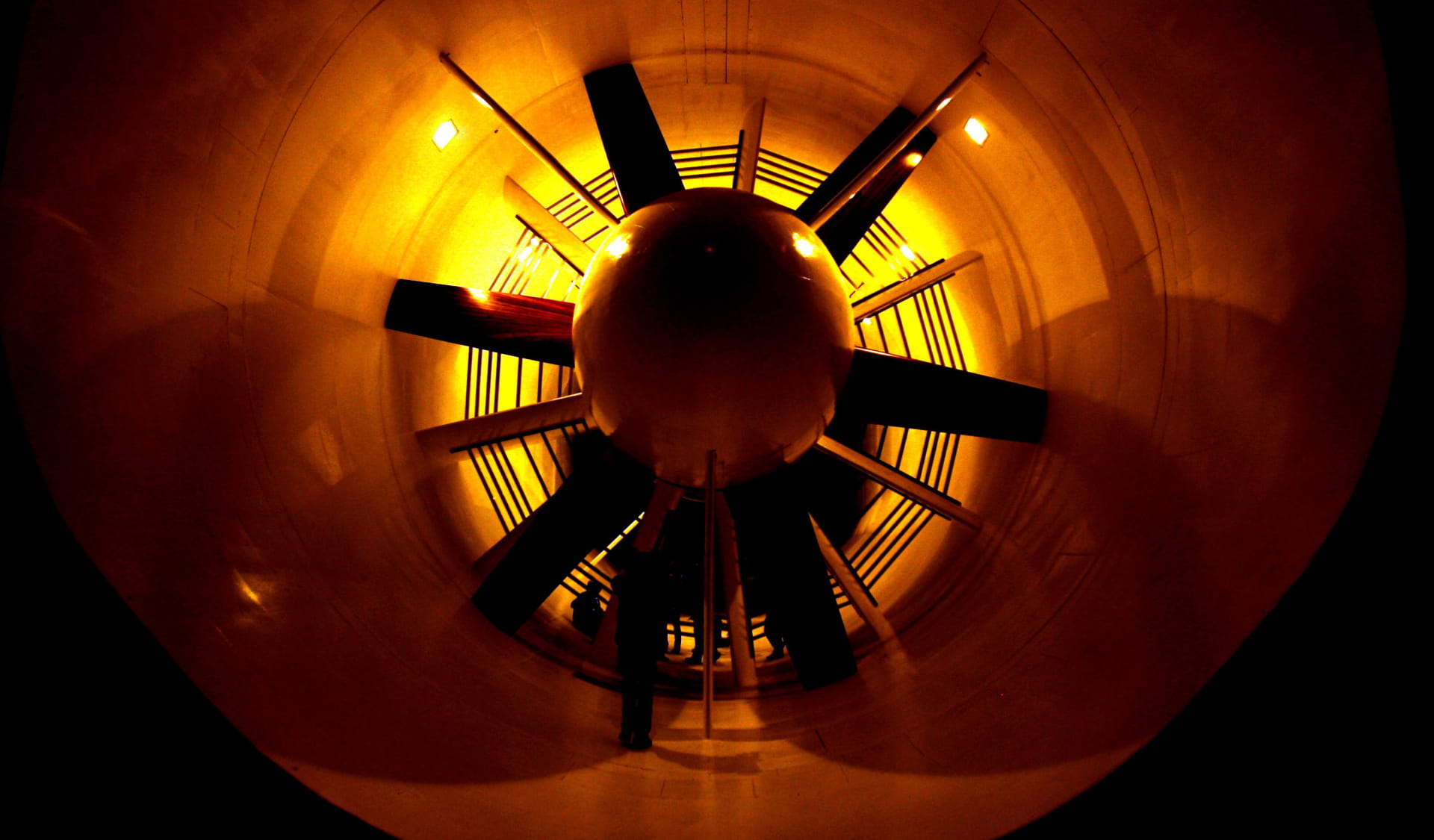
Innovation
Ground effect in F1: How aviation pioneers sparked a motorsport revolution
The arrival of car-mounted wings was the first step into an era where aerodynamics would become highly significant, and eventually the dominating factor, in top-flight circuit-racing car design, and an increasingly important factor in other categories such as rallying.
In formulae where car design – albeit following tight regulations – is down to the individual team/manufacturer, aerodynamics has also become the primary focus of development work during the season, as in the majority of racing categories, aerodynamic improvements can see higher gains in terms of reduced lap times than any other area of development.

A scale-model of a Mercedes Formula 1 car in a wind tunnel. The F1 technical regulations allow for a 60% scale model of a car to be used for wind tunnels
Drag and downforce
There are two essential factors involved in racing car aerodynamics:
Drag – a force that acts in the opposite direction to the motion of an object. In this case, the object is the car, and the fluid is air.
Downforce – a force that acts downwards on an object.
Aerodynamicists therefore aim to reduce drag, allowing the car to move through the air more freely and faster, and to use aerodynamic devices such as wings to generate downforce.
Today’s F1 and WEC cars generate extremely high levels of downforce, and at high speed the level of downforce produced can exceed the car’s weight. An F1 car at top speed can generate four times as much downforce as its weight.
Aerodynamic forces generated are dependent on speed - although levels of drag and downforce are not dependent on speed. For a doubling of the car’s speed, aerodynamic forces increase by a factor of four.
Balancing drag and downforce is a compromise for designers. Compared with a road car, a racing car actually has a relatively high drag factor - due mostly to the size of the wings.
If the driver lifts off the throttle in a current F1 car, set up to run on a ‘high-downforce’ track such as the Hungaroring in Hungary, over 1G of deceleration is produced without touching the brakes.
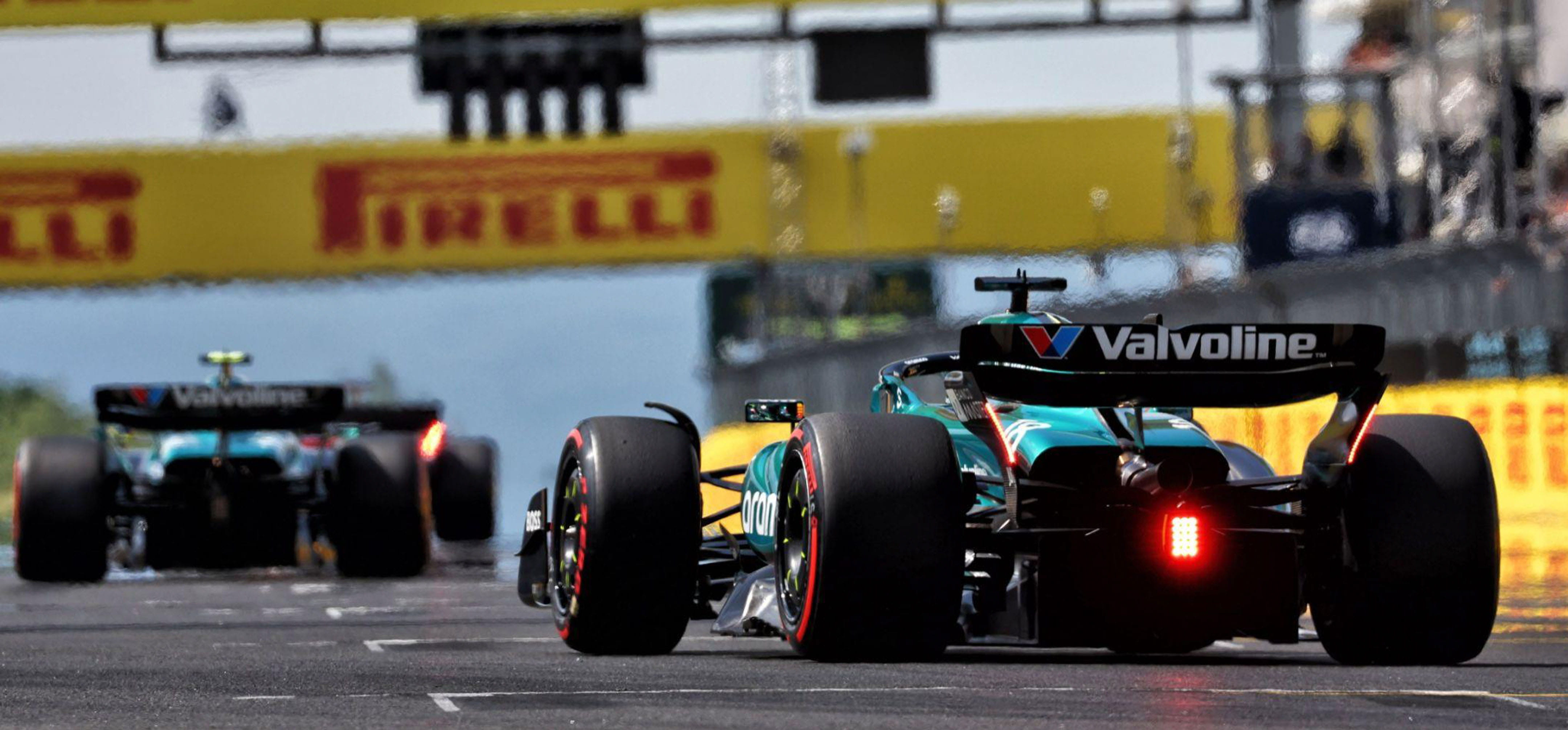
Large amounts of drag mean F1 cars can decelerate significantly without the use of brakes
Aerodynamic design is not solely concerned with minimising drag, which would optimise speed in a straight line, and maximising downforce, which would achieve higher cornering speeds. It is also crucial to aim for aerodynamic stability in order to ensure consistent downforce.
Aerodynamic instability can lead to significant handling problems and the driver’s loss of confidence in the car, which leads to slower laptimes.
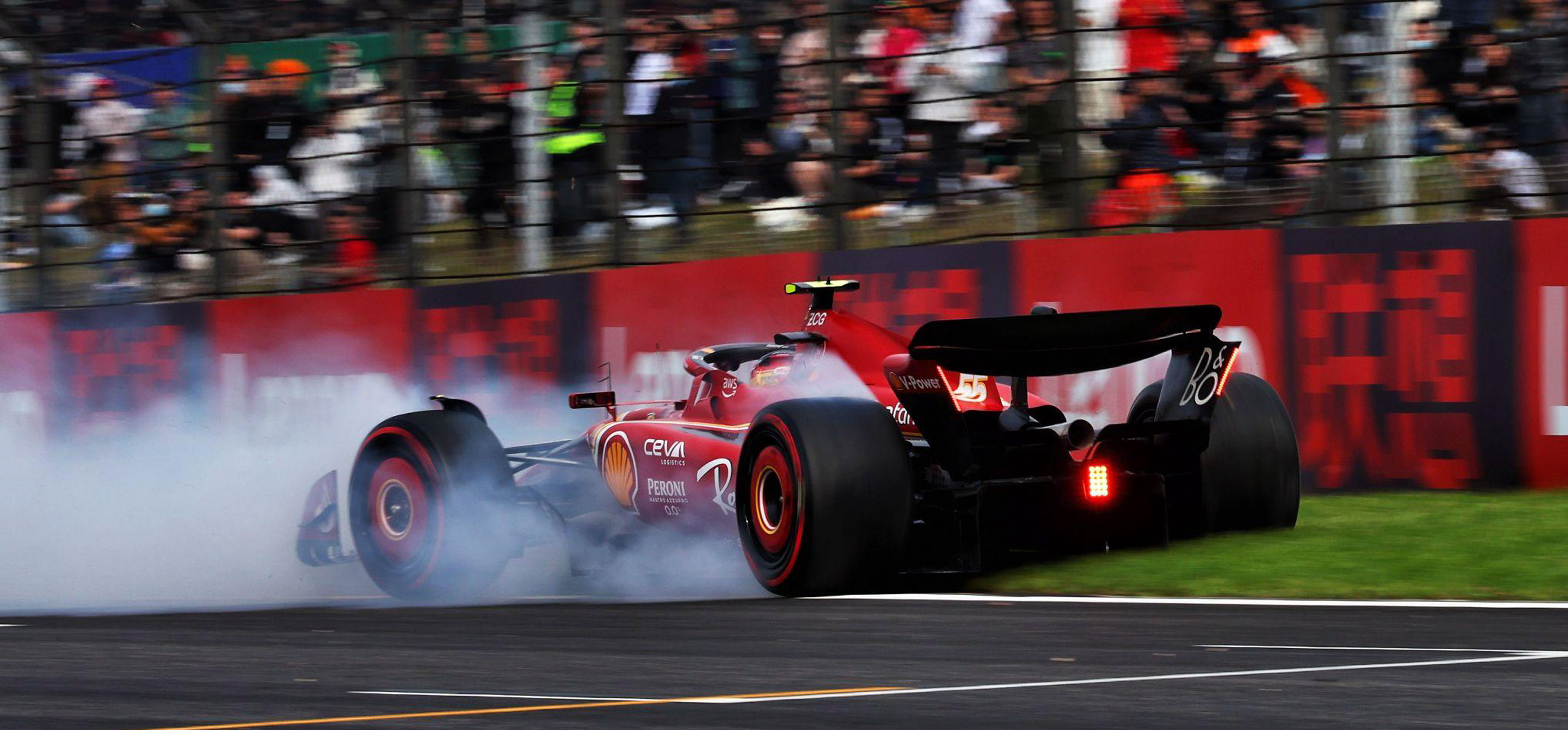
Instability can lead to handling problems and even spins and crashes
How wings are used to produce downforce
The wings on a racing car operate in exactly the same way as an aircraft wing, except that on the cars, the wings are mounted upside down - generating downforce rather than lift.
Downforce is generated when there is an area of high pressure airflow above a surface and low pressure airflow below the surface.
The shape of a car’s wing - essentially an upside down aerofoil - generates downforce because air flowing under the wing has to travel further than the air flowing over the top of a wing.
Bernoulli's principle states that an increase in the speed of a fluid corresponds with a decrease in pressure. Therefore, with a low pressure zone under the wing and a high pressure zone above the wing, downforce is generated.
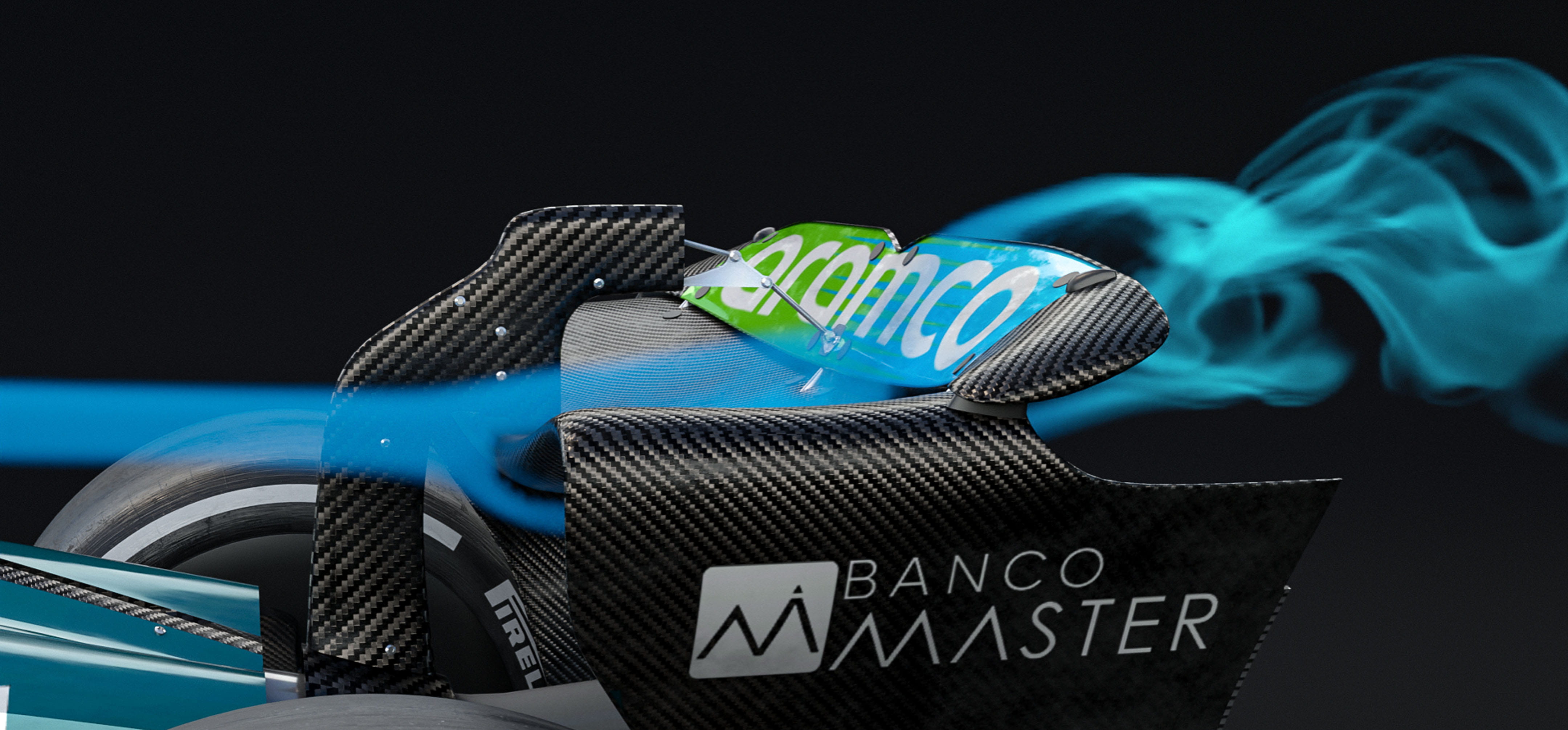
With low pressure flow under the wing and high pressure above the wing, downforce is generated
Why does aerodynamic ‘stalling’ occur?
There is a slight complication in that, as air flows across the wing, that air tends to separate from the lower surface of the wing - increasing the amount of drag acting on the wing.
Flow separation occurs when the smooth flow of a fluid (air or water) gets disrupted: the fluid starts to flow backwards or form a ‘swirling’ pattern. Generally, this occurs because an increase in pressure causes the fluid to detach from the surface.
This causes the wing to ‘stall’, resulting in a sudden loss of downforce and drag.
If the wing stalls unexpectedly, this can have a sudden negative effect on the car’s handling through corners. The Drag Reduction System (DRS) does cause a stall in airflow, but this is expected and, in this case, the device is used as an overtaking aid in certain predetermined areas of a circuit in Formula 3, Formula 2, and F1.
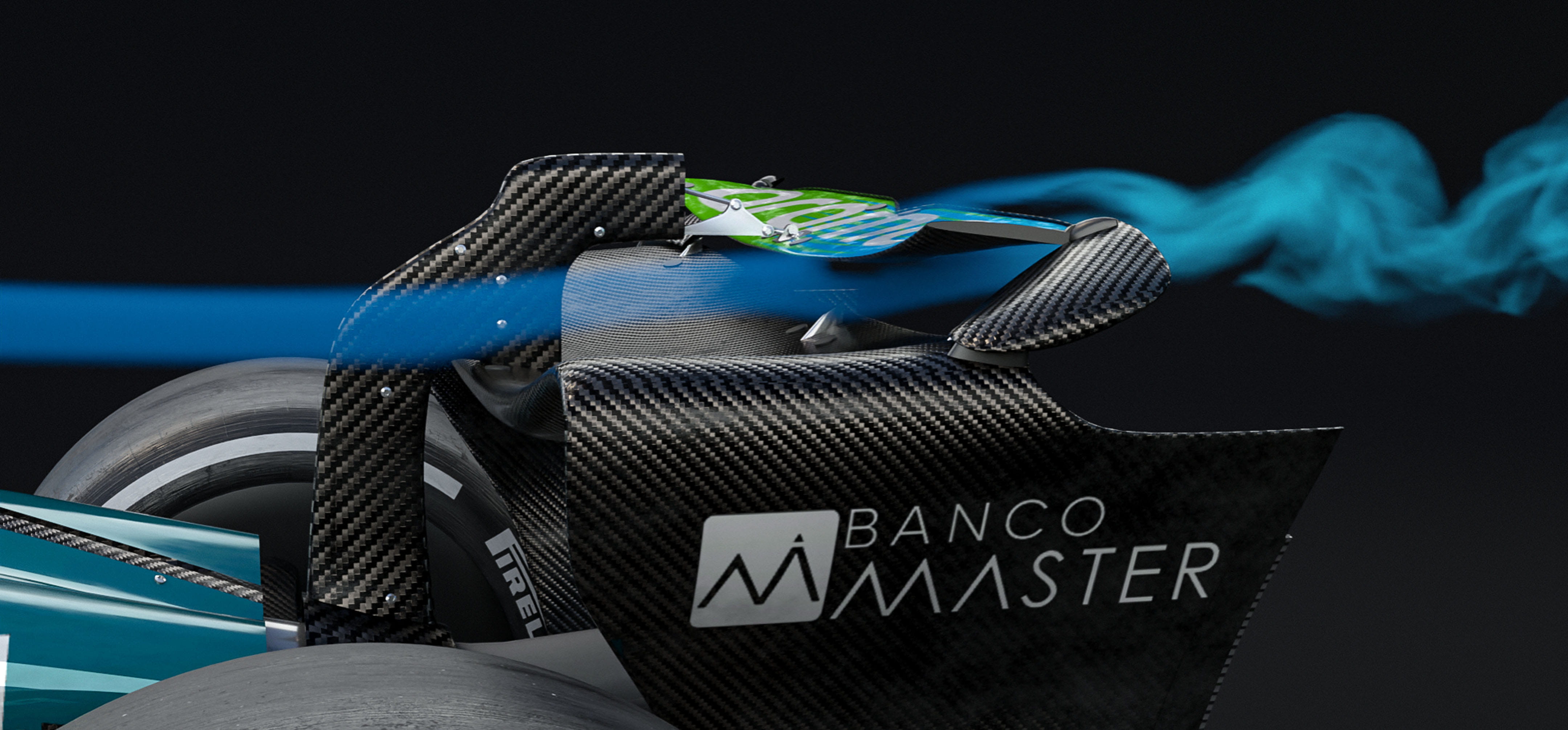
Simulation showing airflow over a rear wing with DRS open
The steeper the angle of the rear wing, the higher the level of downforce it will produce, but with that benefit comes a higher risk of flow separation and therefore stalling.
To reduce the tendency of the wing to stall, the air flowing under the wing must be speeded up, which can be achieved by splitting the wing section into two separate elements, with a slot between them.
With this arrangement, the high-pressure air flowing across the top of the main element can pass through the slot, which helps to speed up the air flowing underneath the element. As a general rule, using a greater number of slots and wing elements enables the main element to be positioned at a steeper angle, generating more downforce.
In many racing categories, the number of wing elements is restricted by the regulations.
What is a diffuser - and how does it work?
Again, depending on the category, various aerodynamic devices other than wings may be used, and as the various components interact, it means that they must be designed to work as a system, rather than in isolation.
In terms of efficiency, it is difficult to design front and rear wings to produce increased downforce without also increasing drag.
The most efficient aerodynamic component on most cars is a rear diffuser, which can be designed to generate high levels of downforce with minimal drag.
A diffuser generates downforce using the Venturi principle, which in essence involves using a tube, with a constriction partway along its length, to accelerate air and reduce its pressure.

Simulation of flow under a diffuser, an outlet for air flowing from a high-pressure zone to a low-pressure ambient zone
In a racing car context, the air enters the tube at the front of the floor, the area under the floor forms the restriction – the floor configuration varying depending on the relevant regulations – and the diffuser forms the air outlet.
By careful design of the floor and diffuser and, again depending on the category, the front wing (which controls the airflow over the surfaces of the car behind it), the air under the car can be accelerated, lowering its pressure and therefore producing downforce.
Numerous other aerodynamic devices may be fitted, but, as mentioned previously, they must all be designed to work in harmony, reducing drag and creating downforce, while helping to optimise the handling of the car to enable the driver to push it to its performance limit.
Aerodynamic set-up today is every bit as important as mechanical set-up, and in fact is arguably more important for some formulae. But for all formulae, achieving optimum aerodynamic performance and consistency is absolutely key to car performance.