Future
Inside the new Aston Martin Aramco Formula 1 Team factory
by Samarth Kanal
12min read
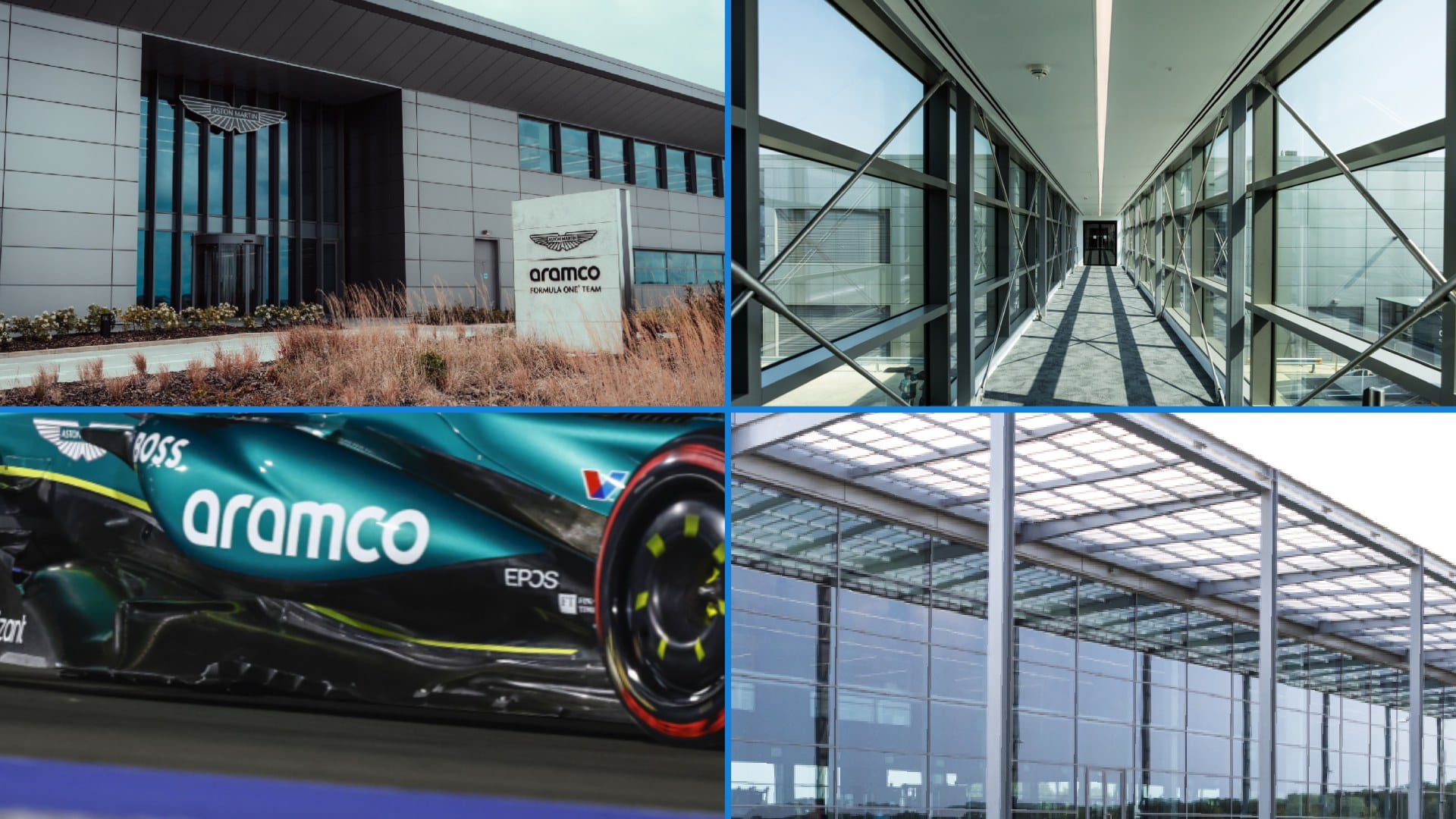
The newest factory in Formula 1 is almost complete. Aston Martin Aramco F1 Team is about to reap the rewards of its expanded headquarters, located just across the road from Britain’s Silverstone Circuit.
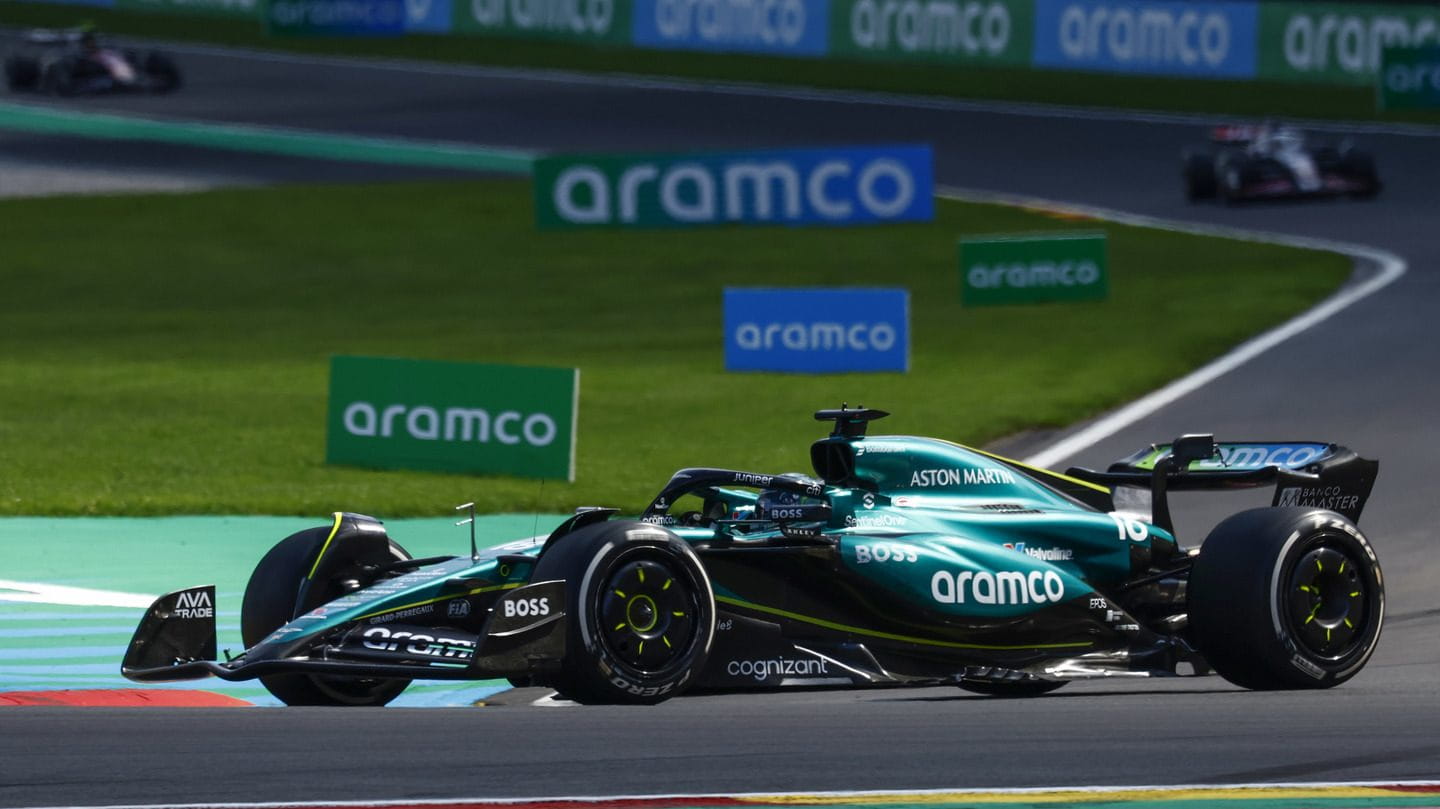
Partner content
The Aramco and Aston Martin Racing strategic partnership
That was one of our biggest struggles: to remove the shackles, literally think ‘utopia’
Tom McCullough
, Ex-performance director, Aston Martin Aramco
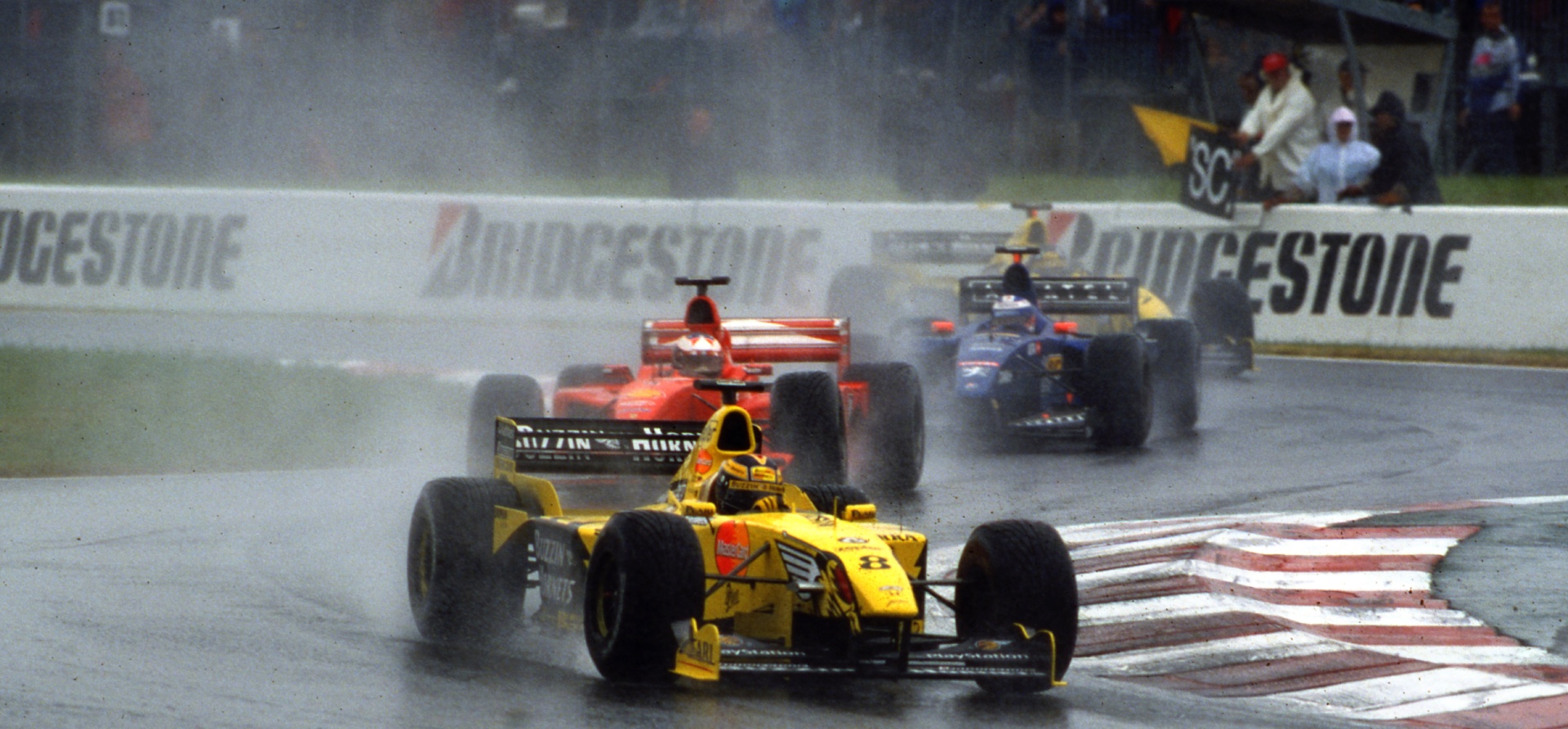
Heinz Harald-Frentzen on his way to victory in the 1999 French Grand Prix. Cars built by ‘Team Silverstone’ won five races, most recently in the 2020 Sakhir Grand Prix
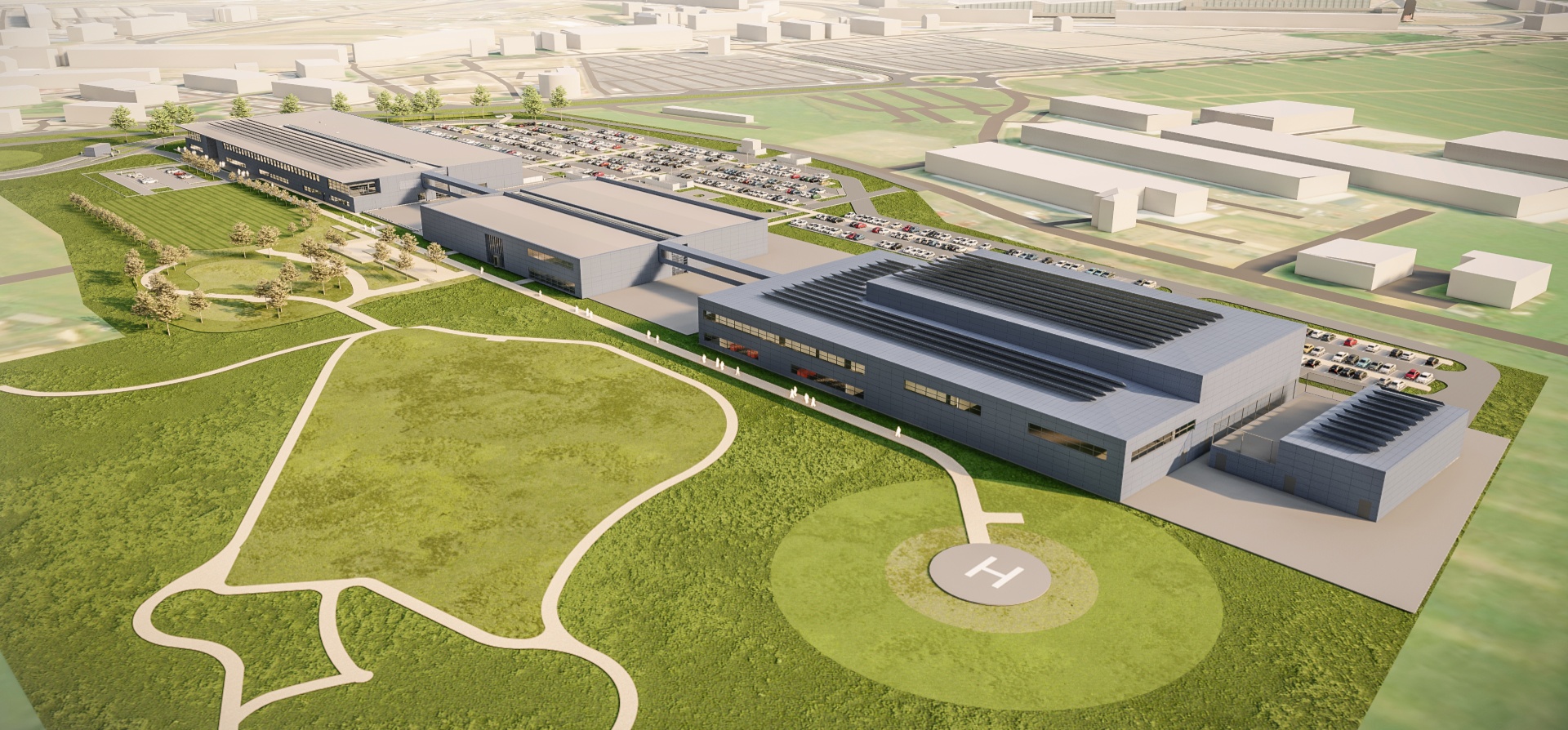
Renders showing plans for the Aston Martin Aramco Formula 1 Team factory, including a helipad, the running track, and three buildings connected by bridges
The timeline and buildings that make up the new factory
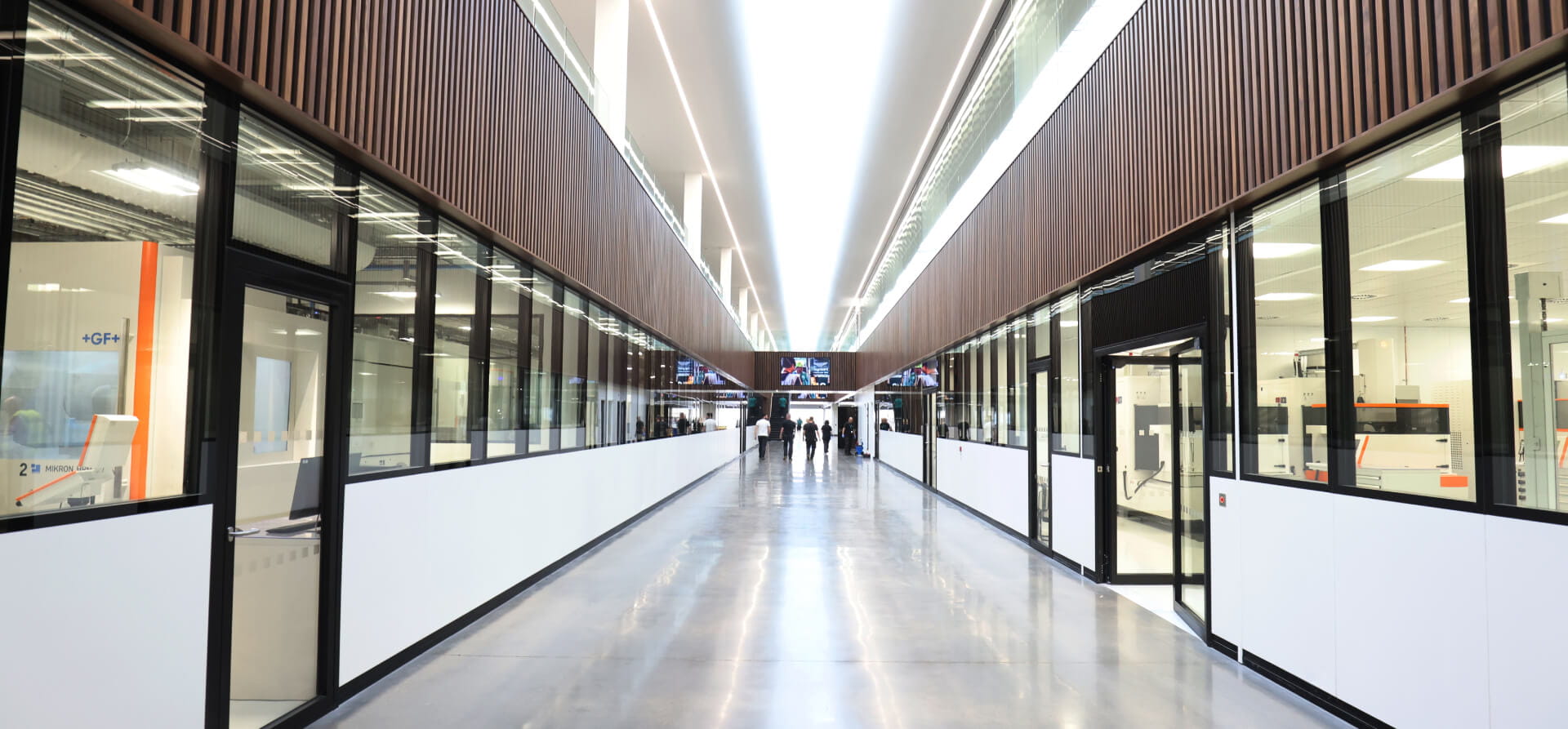
The ‘Street’ on the ground floor of building one in the Aston Martin F1 factory
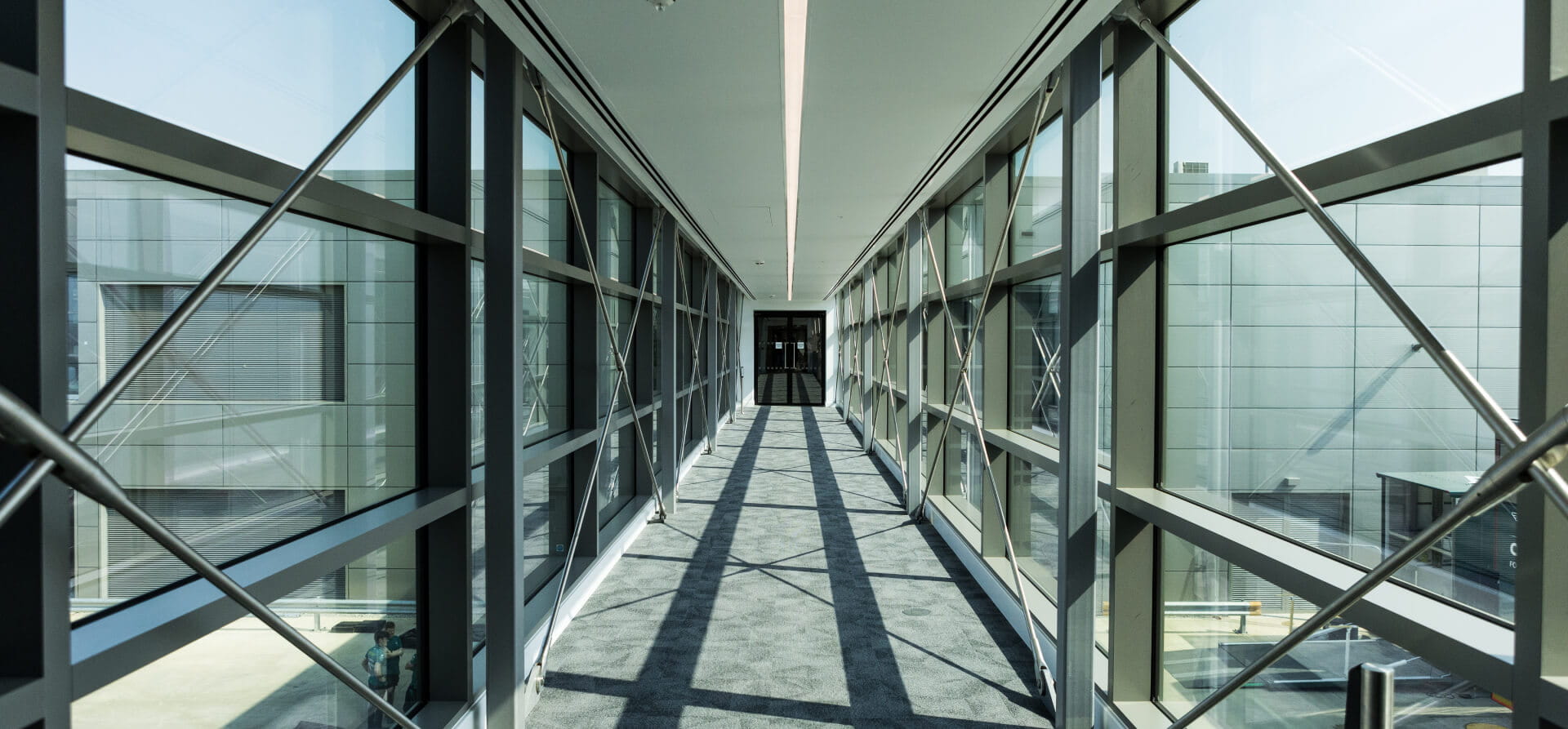
Inside one of the bridges connecting buildings at the Aston Martin F1 factory
One of the issues, of course, is that Formula 1 never stands still
Guy Austin
, project manager, Aston Martin Aramco F1 Team
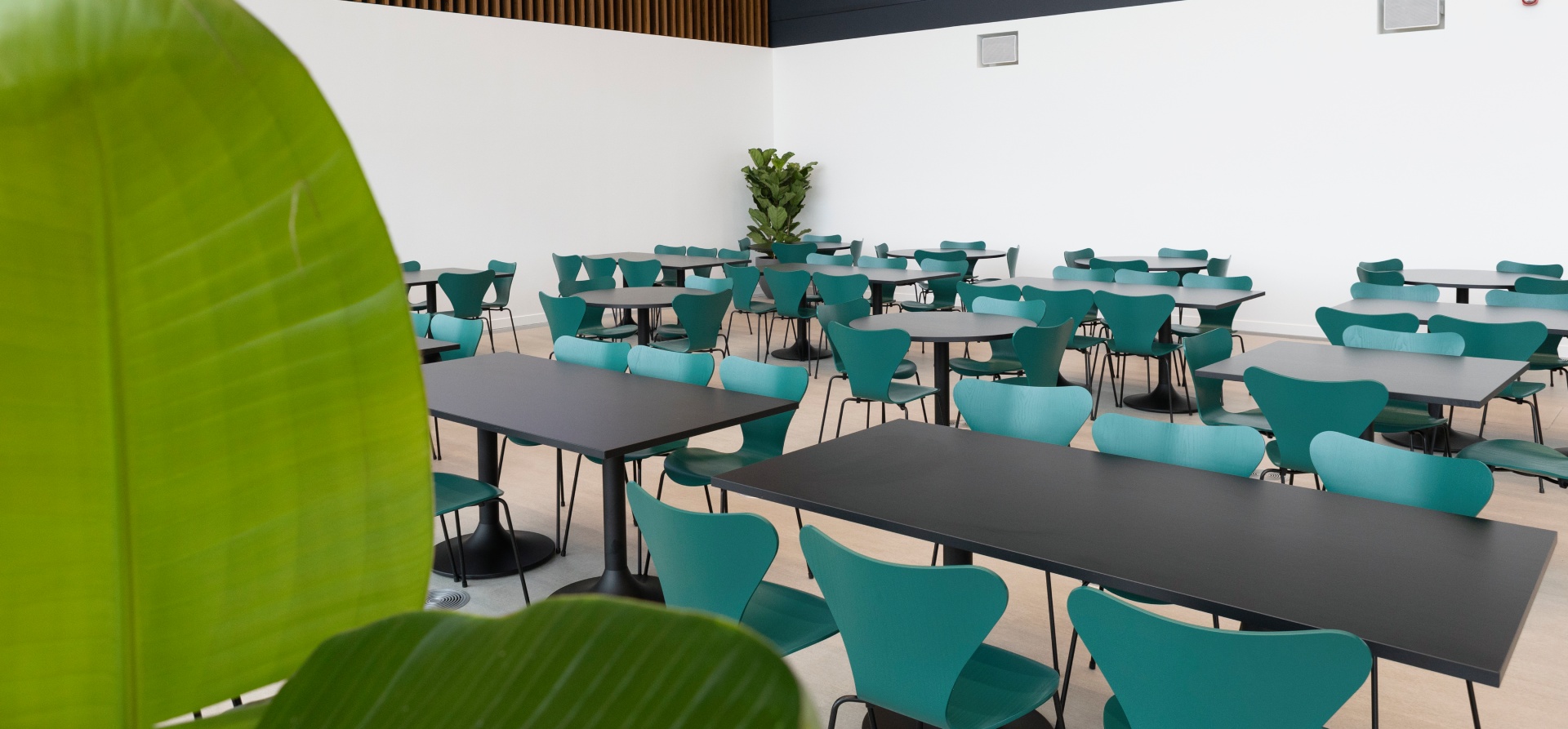
The staff canteen can feed around 300 people - many more than the temporary canteen that was located in the parking lot during construction
The third building includes the model shop, where the windtunnel models are created, with the windtunnel and its control room right next door. With F1’s Aerodynamic Testing Regulations (ATR) limiting the use of windtunnel time, this layout saves crucial time.
.jpg?cx=0.5&cy=0.5)
Adrian Newey (L) with Lawrence Stroll (R) at the team’s announcement event at its factory in September 2024
Quick wins - the short-term gains of the new F1 factory
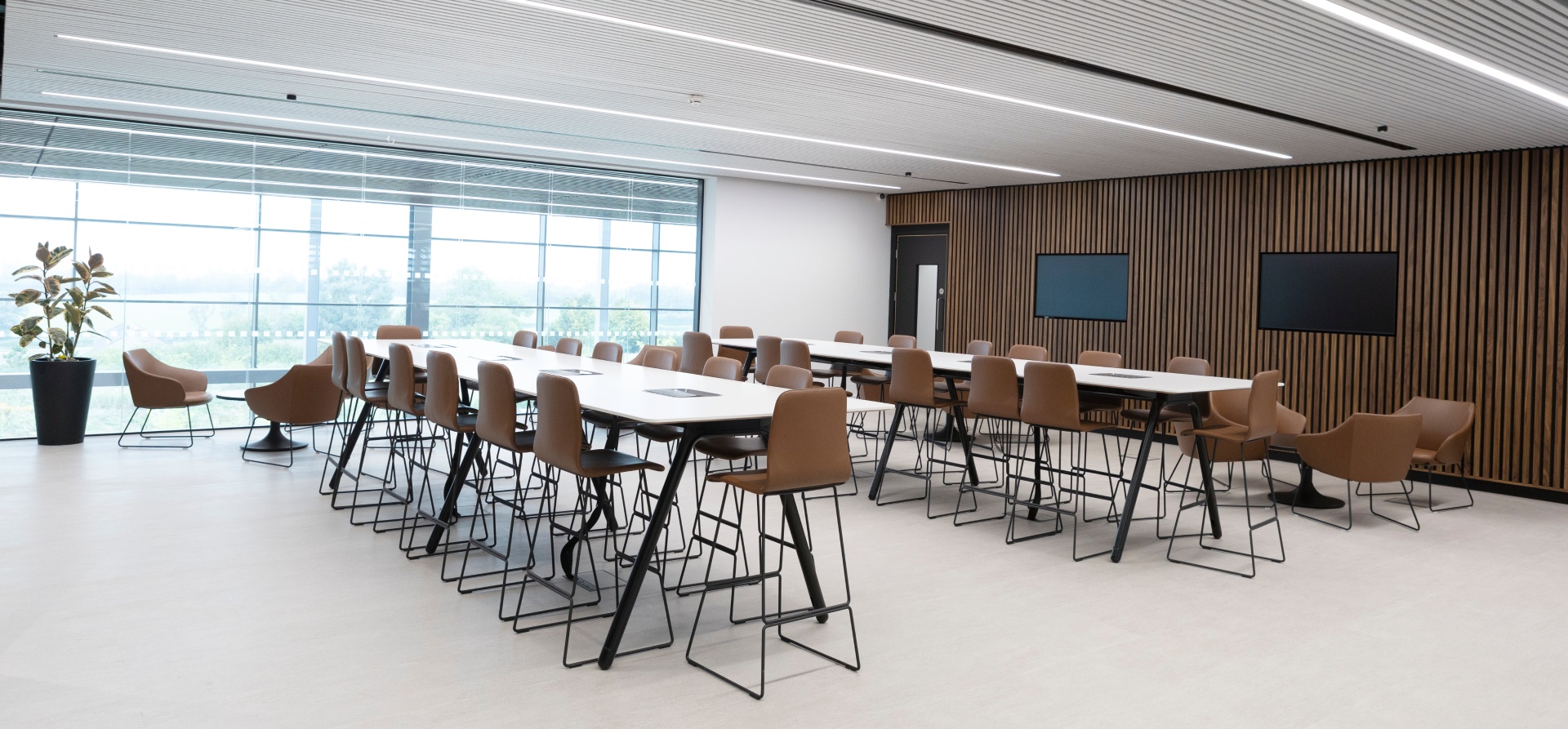
Natural light means nearly every room in the factory is a pleasant place to work - and a step up from the former headquarters
We’d outgrown the infrastructure of the factory. We even cut extra doorways in.
Ben Fitzgerald
, operations director, Aston Martin Aramco F1 Team
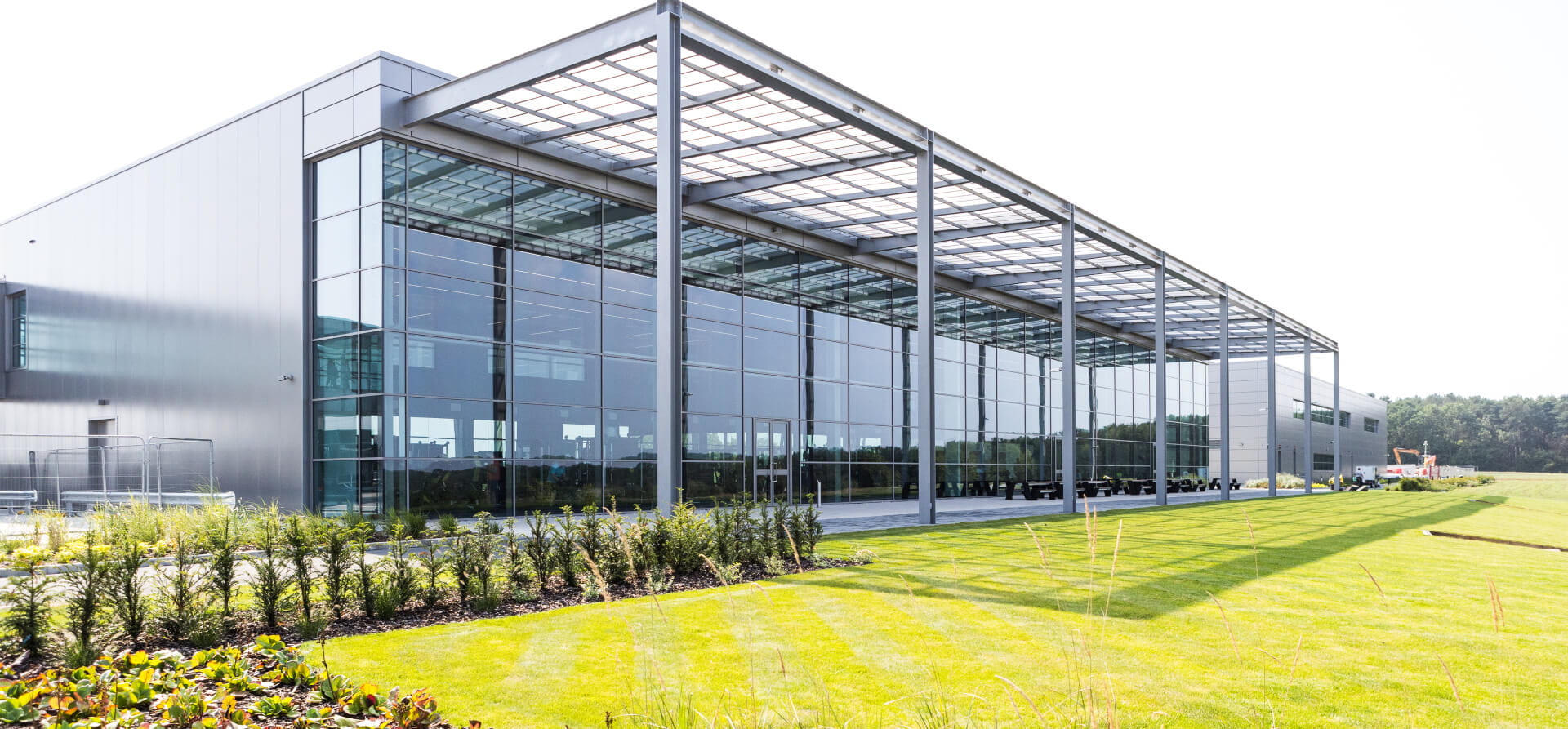
The outside of building two of the Aston Martin F1 factory, where the new simulator is located
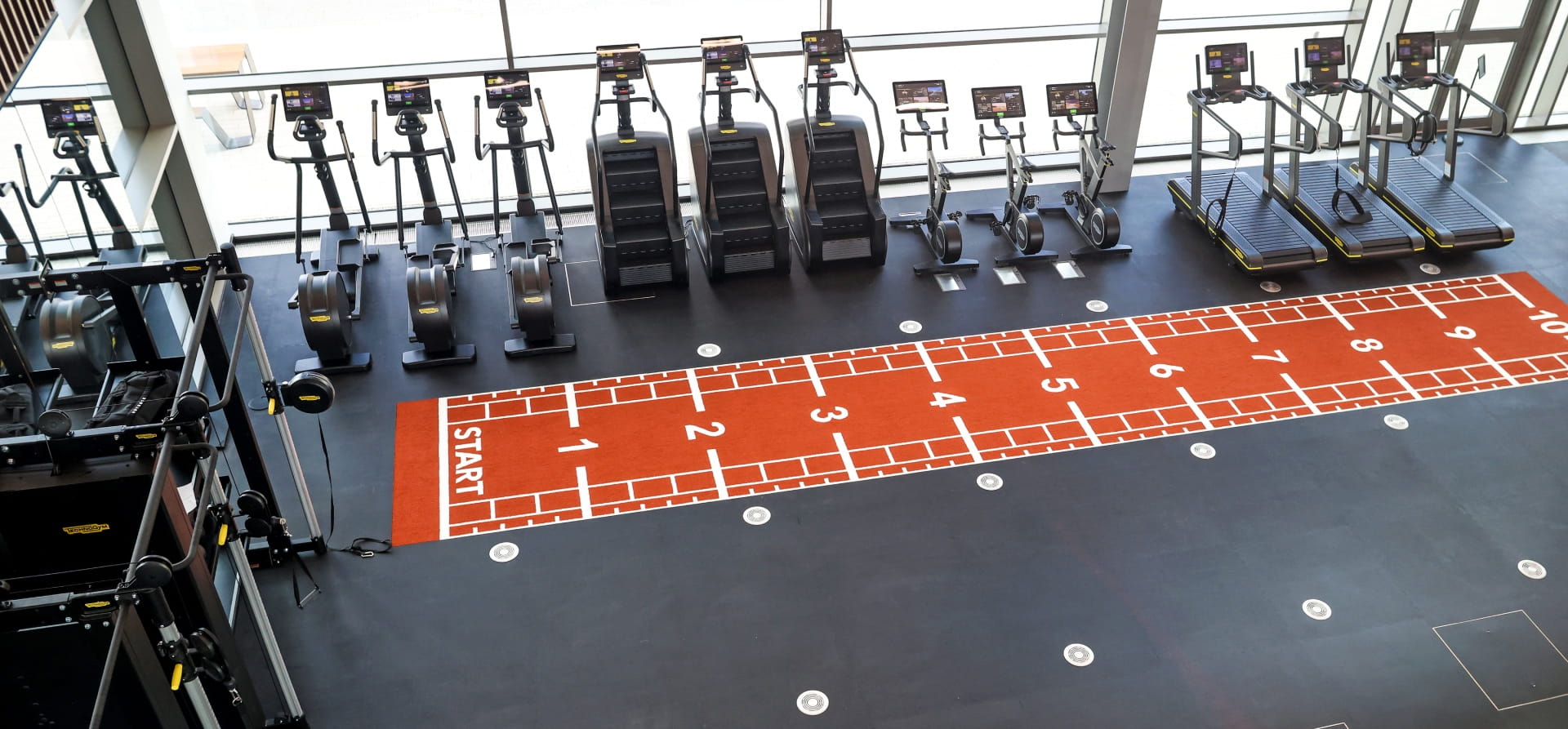
The fitness centre at Aston Martin’s new F1 headquarters
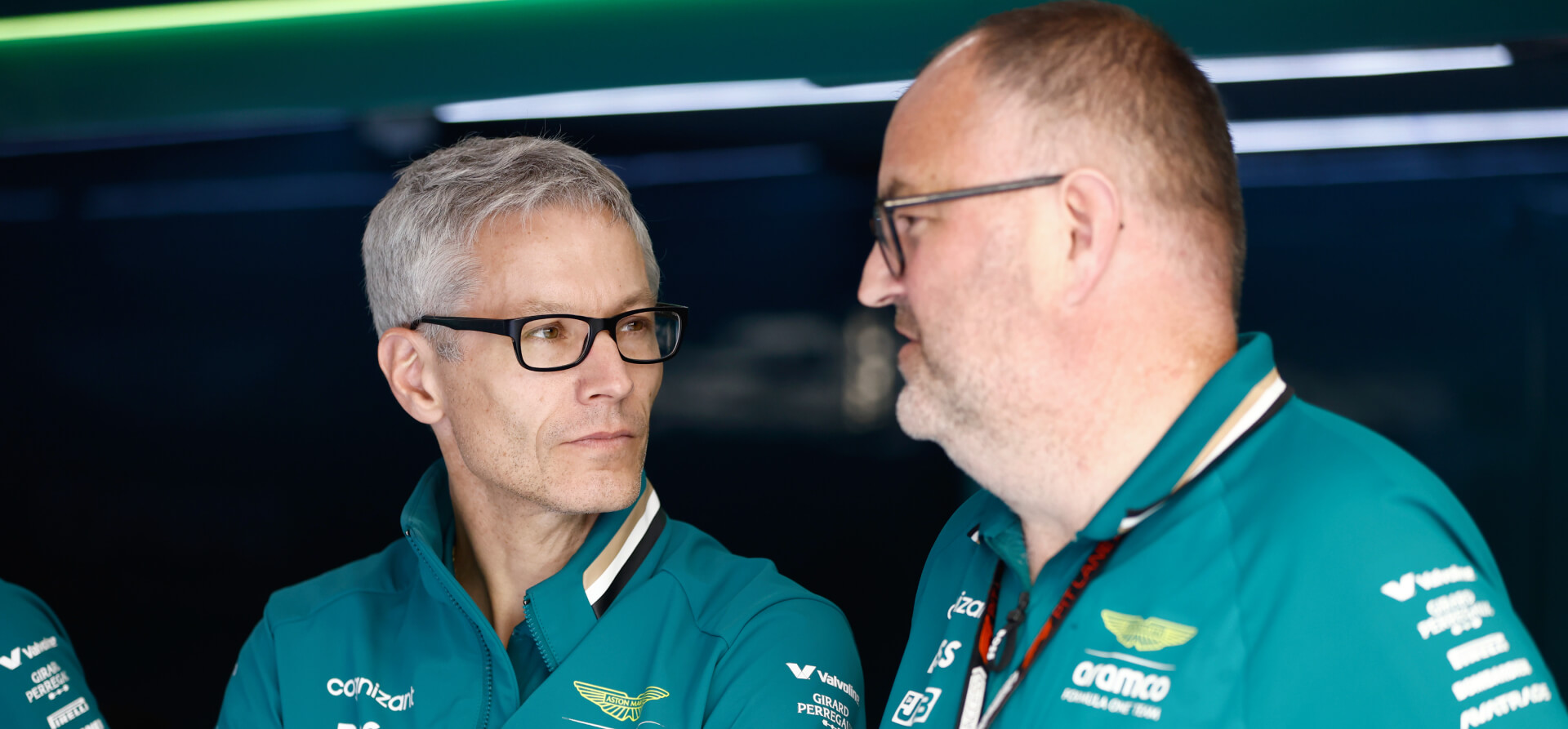
Aston Martin Aramco F1 Team's former team principal Mike Krack (L) and ex-performance director Tom McCullough (R)
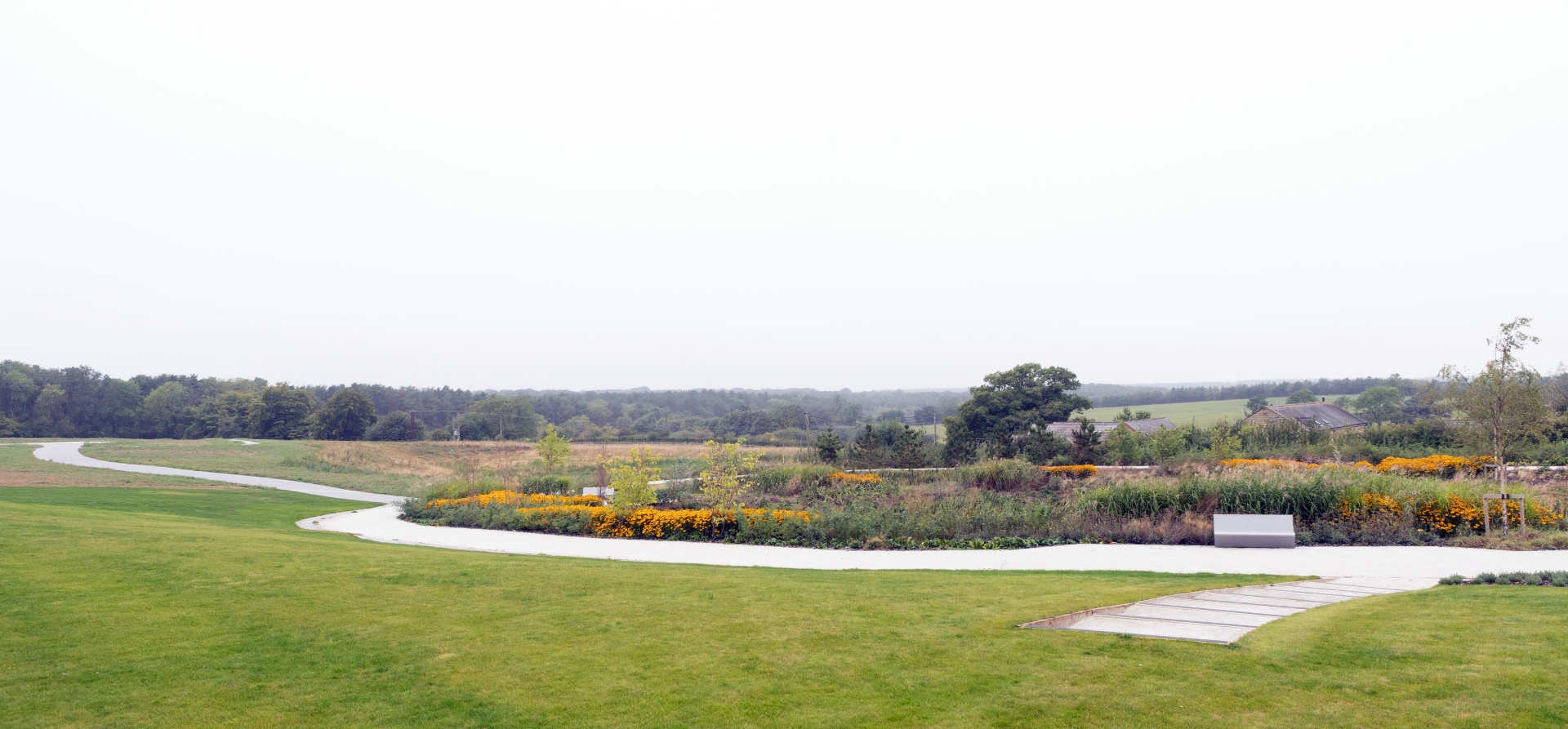
The running track outside Aston Martin’s new F1 factory, with wildflowers at its centre
Environmental and sustainability achievements
Those include ISO 50001, concerning energy consumption and efficiency; ISO 14064, regarding greenhouse gas emissions; and ISO 14001, surrounding environmental management systems.
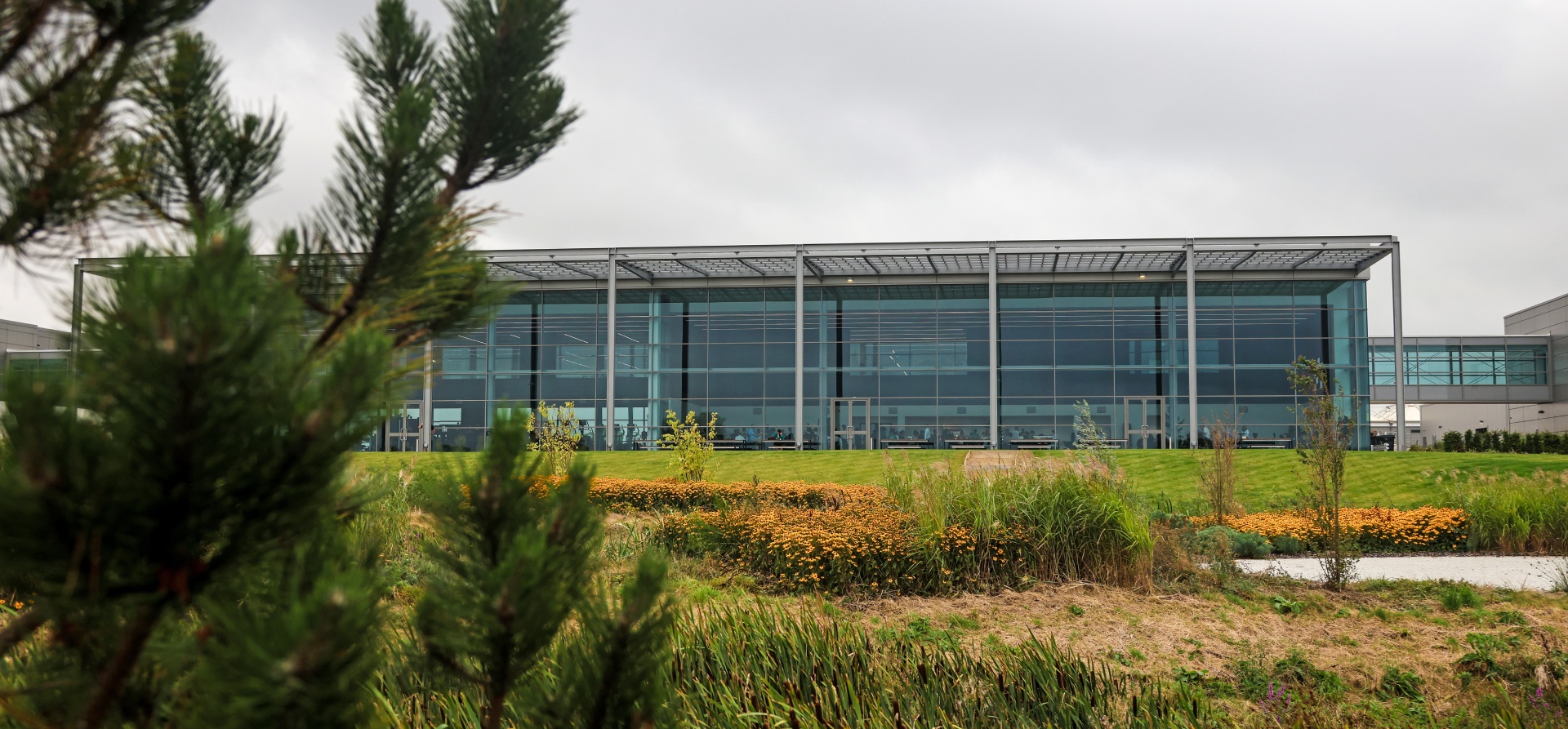
Team owner Lawrence Stroll said sustainability was one of the team’s goals alongside extracting more performance on track
This is not Force India or Racing Point any more, and this is not an underdog project
Mike Krack
, former team principal, Aston Martin Aramco F1 Team
Is this the final piece of the puzzle?
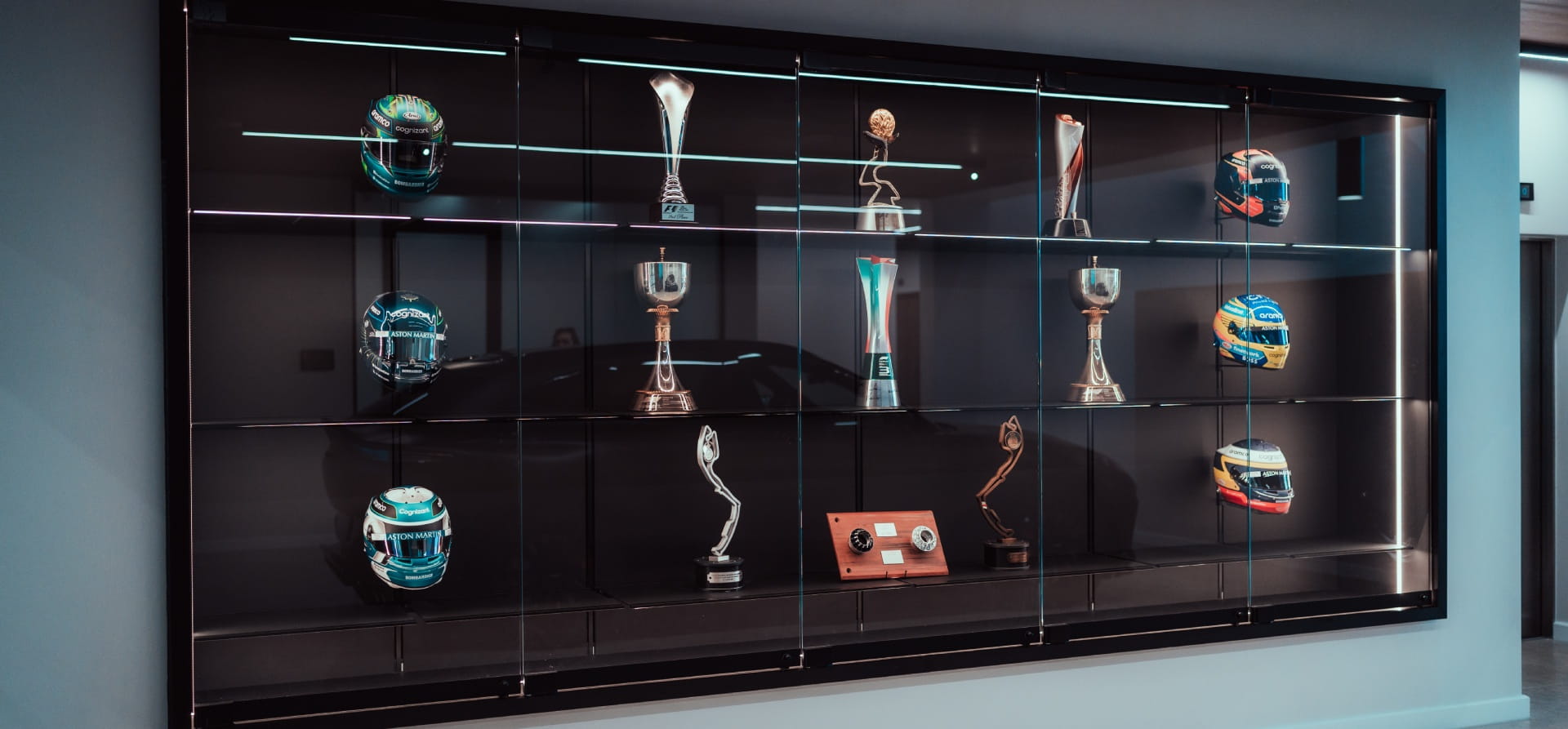
Trophies and memorabilia displayed in the Aston Martin Aramco Formula 1 team factory. As of the end of 2024, the team’s last F1 podium finish was achieved in Brazil in 2023
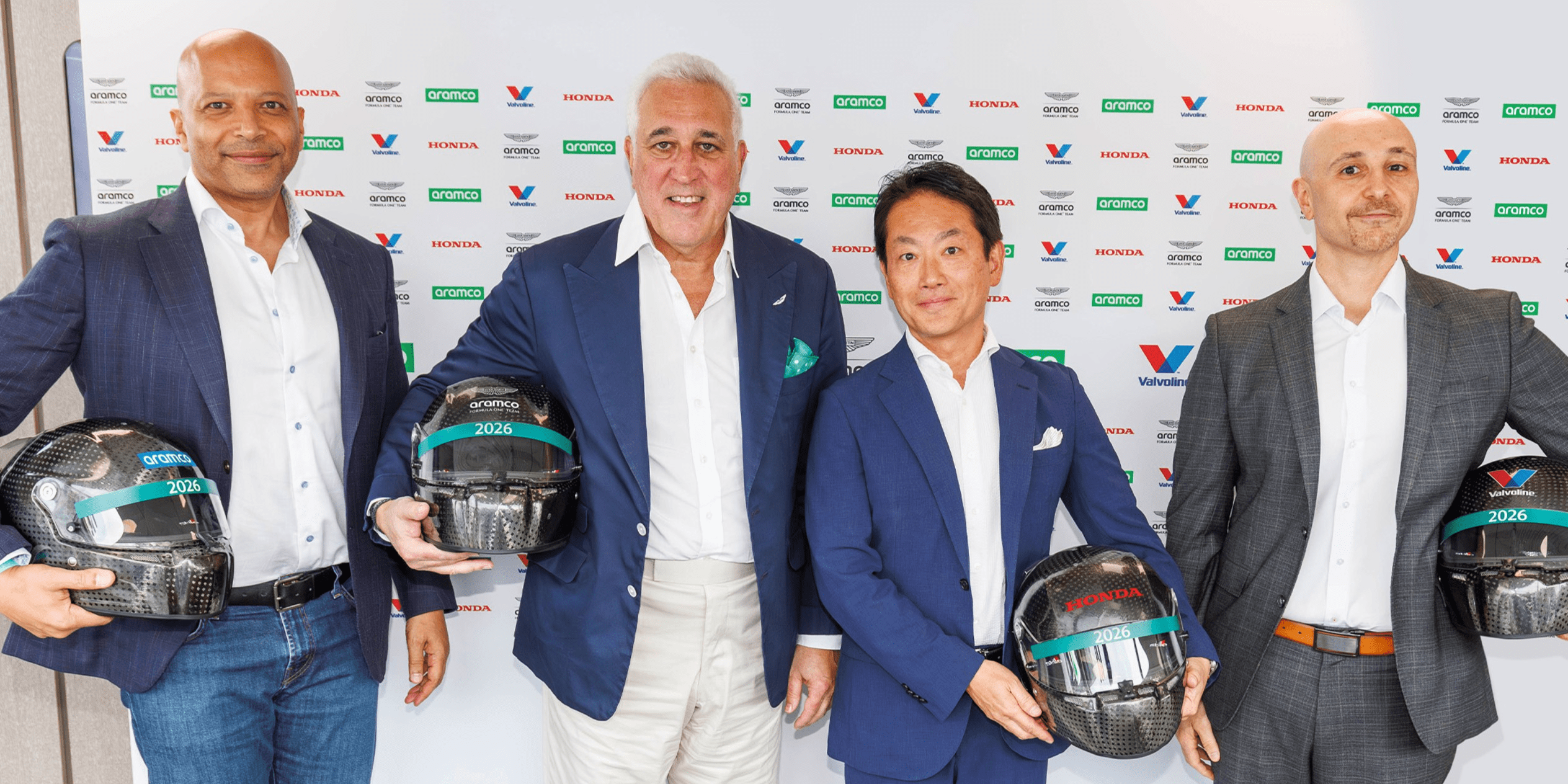
L to R: Aramco executive vice president of products and customers Yasser Mufti, Aston Martin Aramco Formula 1 Team executive chairman Lawrence Stroll, Honda Racing Corporation president Koji Watanabe, Valvoline Global CEO Jamal Muashsher