Innovation
Carbon fibre: How Aramco is innovating material solutions
by Samarth Kanal
8min read
.jpg?cx=0.5&cy=0.5)
Carbon fibre is lightweight and durable - and this makes it suitable to help address growing global energy and material demands. But carbon fibre is energy-intensive to produce. Here's how Aramco is helping find a solution.
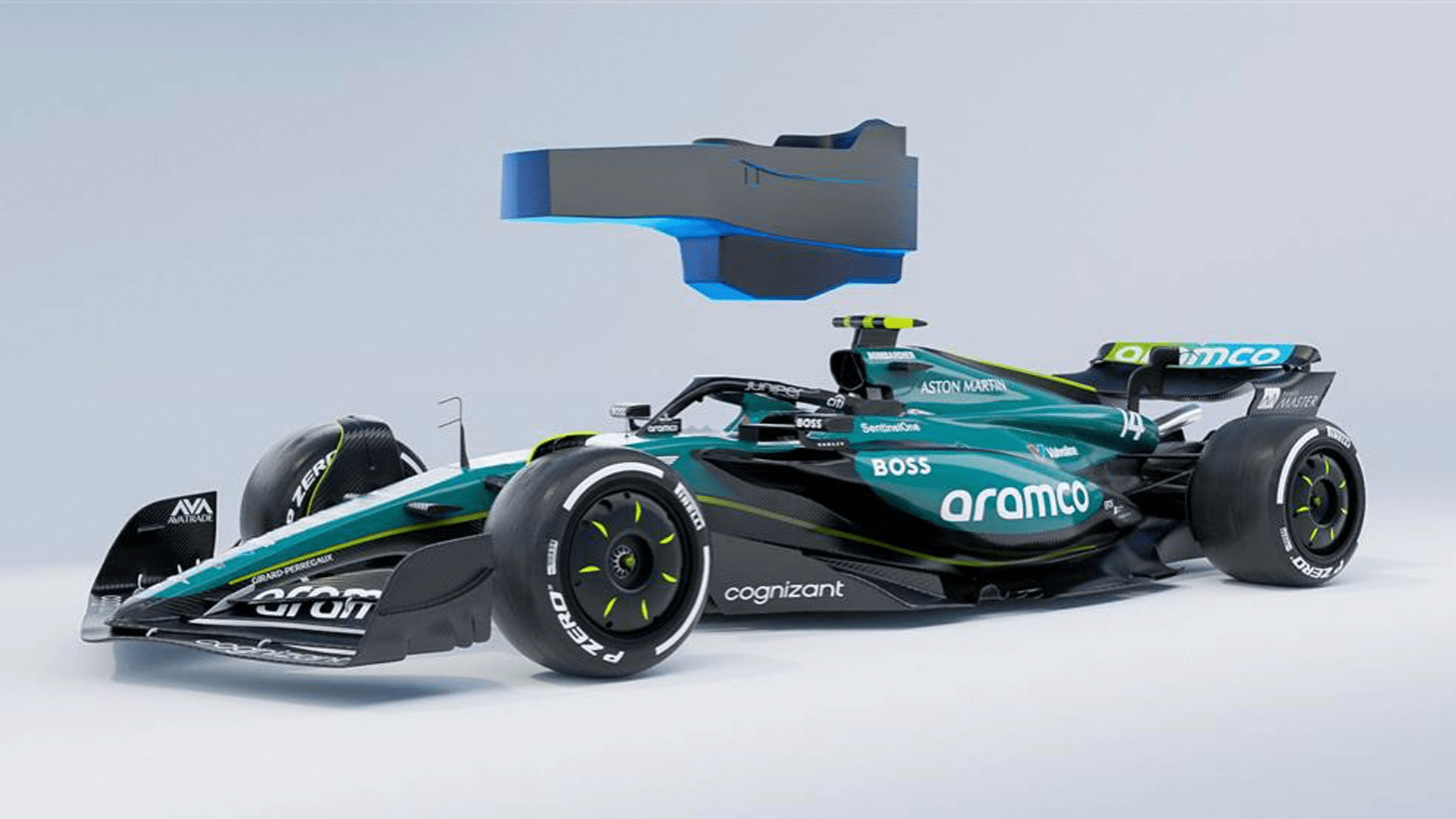
Car, Innovation
The evolution and construction of monocoque chassis in motorsport
Formula 1 cars, spacecrafts, aeroplanes and boats are among the vehicles that use carbon fibre due to its light weight, heat resistance and strength, but these aren't the only uses of this material.
Aramco has pioneered the use of carbon fibre in numerous other applications by focusing on its own operations.
What is carbon fibre?
The carbon fibre we refer to in motorsport and see on the surfaces of racing cars is actually a polymer, and known more formally as carbon fibre-based polymer.
It begins as fibres as thin as five micrometres composed primarily of carbon atoms bonded together parallel to the length of the fibre.
The efficacy of carbon as a construction material had been explored since the late 1800s but in 1963 the United Kingdom's Ministry of Defence patented a process to produce carbon fibre and licensed it to three companies including Rolls-Royce.
Rolls-Royce used the material in the fans for its plane engines but the blades would prove brittle to withstand impacts from birds.
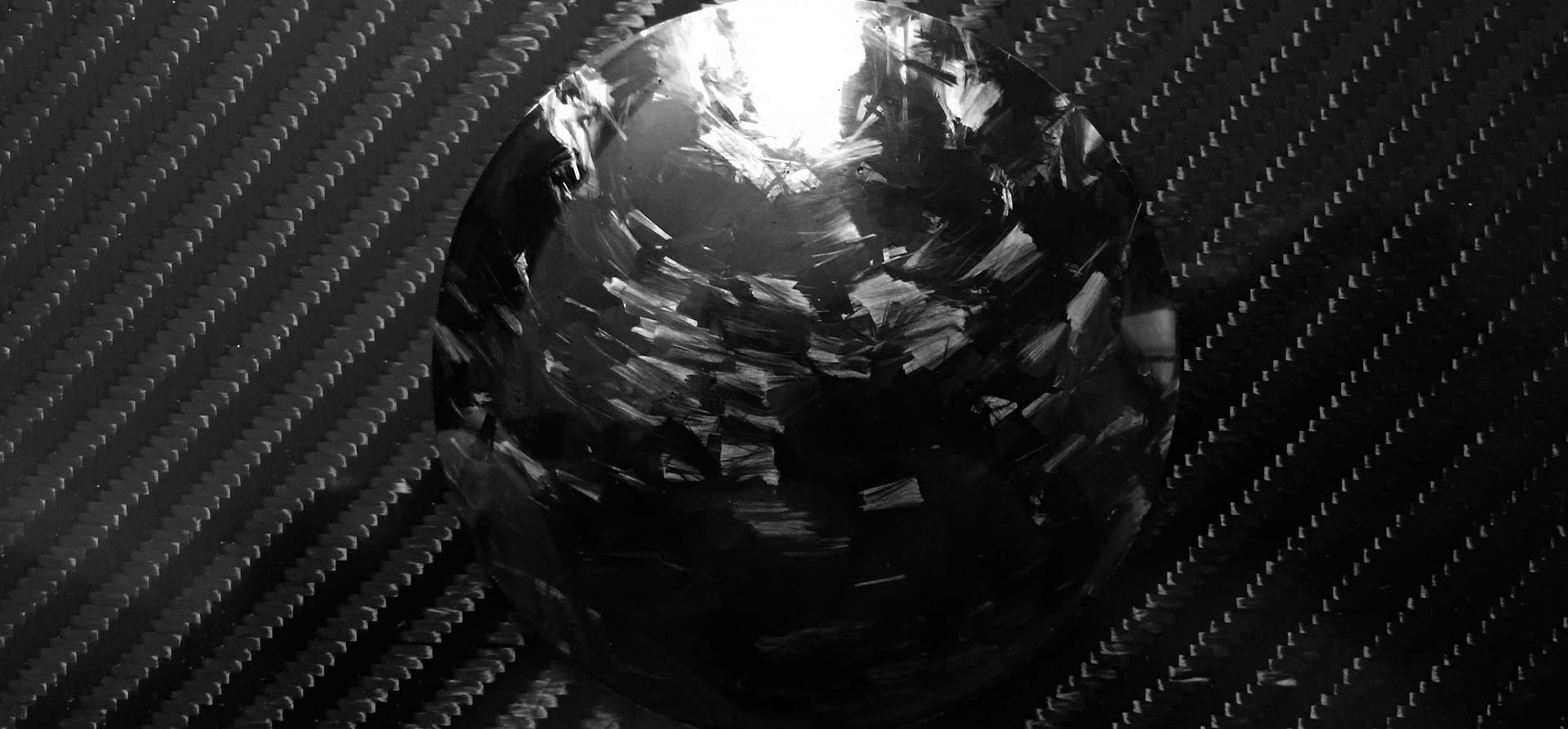
A close-up of carbon fibre used by Rolls Royce in its road cars
Later in the 1960s, companies began to develop the production of carbon fibre - with Japan's government putting in significant investment. In the late 1970s, carbon fibre was developed to have higher tensile strength and in 1981, the McLaren MP4/1 was the first F1 car to be built around a fully carbon fibre chassis.
In 1988, Dupont chemist Jacob Lahjani pioneered a way to increase the strength of carbon fibre further and it would become more prevalent in producing aeroplanes and cars.
Before being processed into carbon fibre-reinforced polymer, carbon fibre itself comes in the form of fabric on a reel. This fabric consists of sheets of carbon atoms arranged in an interlocking hexagonal pattern.
The fabric then needs to be layered - sometimes sprayed or coated with resin to fill the gaps between fibres - and then treated in an oven with temperatures exceeding 1000°C. At times these ovens can reach more than 2200°C to make a product that is even stronger and resistant to heat.
The finished product is often just called carbon fibre, but it can also be known as carbon fibre-reinforced polymer, carbon fibre-reinforced plastic, carbon fibre reinforced-thermoplastic or a carbon composite.
On the surface of a racing car, this carbon fibre has a distinctive pattern - known as a 'weave', depending on the fibres supplied. The weave can actually show the strength and the process that the carbon fibres have gone through before being impregnated by resin.
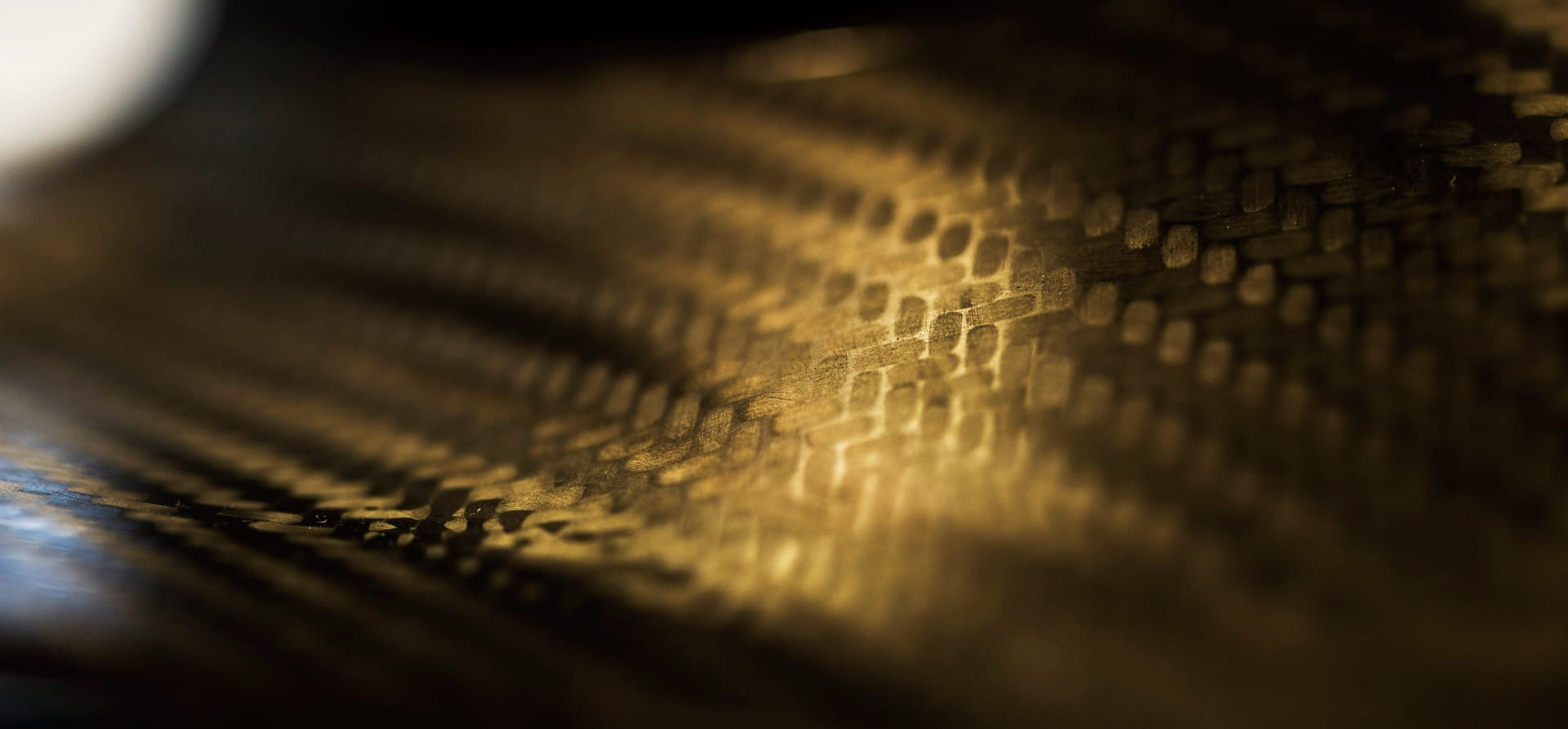
The ‘weave’ visible in a close-up photograph of carbon fibre
Where can carbon fibre be used?
As mentioned, carbon fibre has been used extensively in motorsport including in F1, with chassis, suspension fairings and even race helmets using the material. Sportscars and luxury cars also use the material - often to save weight but sometimes as a 'trim', for vanity purposes.
Aramco has been using carbon fibre-derived materials since 2017 in multiple ways.
In newly drilled oil wells, Aramco uses pipes bonded with carbon fibre due to its ability to withstand high pressures better than steel-based pipes and other nonmetallic composite pipes. Thermal insulation, flexibility, and resistance to corrosion and permeation are some of its other advantages over materials such as steel.
In 2018, Aramco began using carbon fibre to repair existing pipes and control metallic corrosion.
In 2020, Aramco trialled a pipe using carbon composites to transport diesel and petroleum in order to eliminate electrostatic build-up and the chance of static sparks, which can result in fires or explosions.
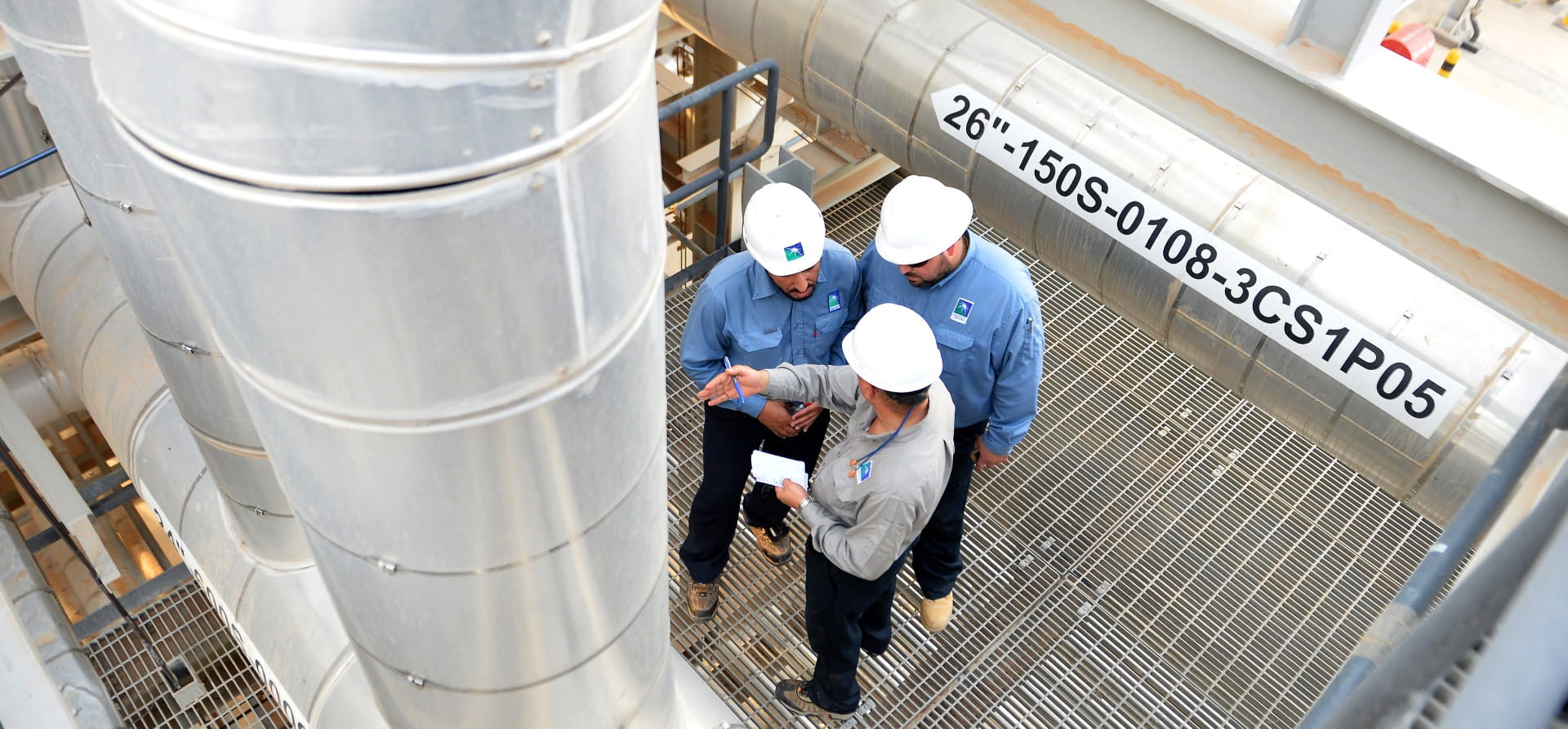
Aramco operators at an oil plant
Reducing the energy consumption of carbon fibre
Strong carbon fibre polymer is energy-intensive and therefore expensive to produce, as it requires furnaces to reach temperatures of 1500°C to purify the carbon fibre.
Furthermore, tools used to cut carbon fibre-reinforced plastics undergo extensive wear (depending on the angle they cut relative to the fibres) because of the strength and forces needed to machine the product.
However, Aramco is working with several partners to help reduce the energy and cost related to producing carbon fibre polymer by up to 50% in some cases.
Aramco has also collaborated with the Institute of Textile Technology in Germany to help increase demand for polymer-based technologies for mass-market applications.
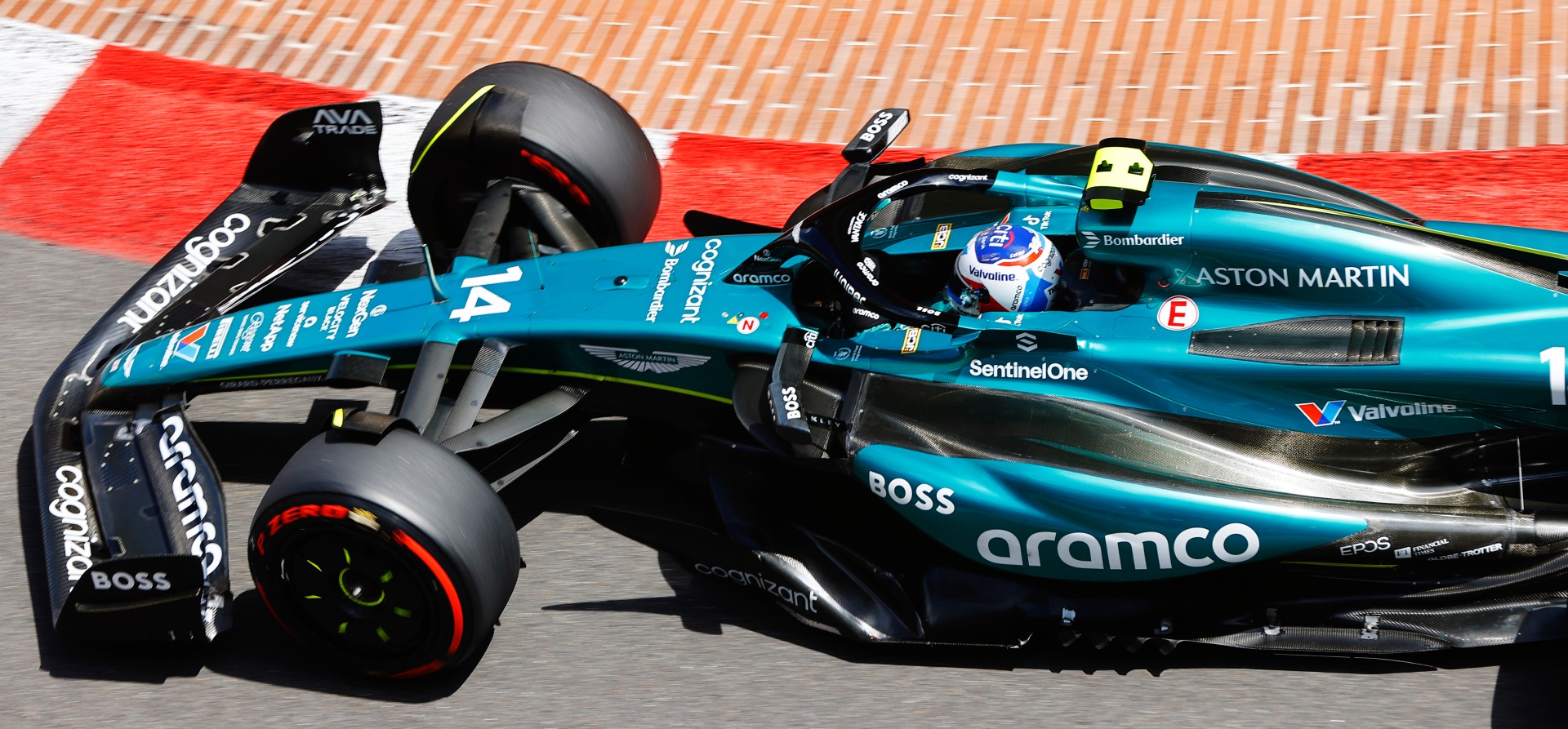
Carbon fibre visible (in black) on the Aston Martin Aramco Formula 1 Team AMR24 at the 2024 Monaco Grand Prix
Project Amiral is a plant being built in a partnership between Aramco, INEOS and Total in Jubail, Saudi Arabia. This plant is expected to focus on the manufacturer of acrylonitrile, a building block for many plastics including polyacrylonitrile (PAN), which is an essential component of carbon fibre.
Once operational, this project has the potential to enable the production of PAN at a lower cost and therefore lower the cost of producing carbon fibre.
Aramco's Carbon Fibre Manufacturing Investment team is also working with potential international partners to establish a dedicated carbon fibre manufacturing facility through Aramco Namaat in Saudi Arabia.
Carbon fibre is a material essential to enhancing safety and laptimes within motorsport, but it also has numerous applications in other industries. Aramco is leading the way to apply the material across its operations, help optimise its production and reduce its costs.